14/11/08 Saturday 14:28
製作( Trial and Error )
目次
パーツ検品
19.フロント・ノーズ・カウル改造編途中経過
18.ステアリング・ロッド、自作編途中経過
17.フロント・サスペンション・アッパー・アーム用ブラケット改造編途中経過
16.ホイール・ハブ・リング自作編途中経過
15.モノコック・フロント・プレート、ディテールアップ編途中経過
14.フロント・サスペンション・アッパー・アーム、ディテールアップ編計画中止
13.ステアリング・ロッド、ディテールアップ編計画中止
12.ゴミ防止網、ディテールアップ編途中経過
11.インター・クーラー、ディテールアップ編途中経過
10.ラジエータ、ディテールアップ編途中経過
9.フロント・ウイング翼端板ディテールアップ編
8.リア・ウイング・ディテールアップ編計画中止
7.フロント・ウイング・ノーズ・ディテールアップ編計画中止
6.エンジン・ブロック・結晶塗装・ディテールアップ編再考中
5.カーボン・ブレーキ・ローター・ディテールアップ編途中経過
4.フロント・ウイング・スキッド自作編
3.フロント・ウイング・翼端板自作編計画中止
2.タイヤ・マーキング・ディテールアップ編計画中止
1.自作デカールについての考察
---------------------------------------------------------------------------------------
フロント・ノーズ・カウル改造編(途中経過)
1.以前、フロント・サスペンション・アッパー・アームの取り付け位置が破綻していると考え、改造を計画。
2.しかし、ボディ・カウルの形状を見て計画を変更することにしました。
3.下の写真を見るとノーズ・コーンとモノコックのつなぎ目とフロント・カウルのつなぎ目を確認。
4.フロント・カウルのつなぎ目がマルボロ・レッド・カラーの部分に存在します。
5.更に、ノーズ・コーンとモノコックのつなぎ目より後方に位置します。
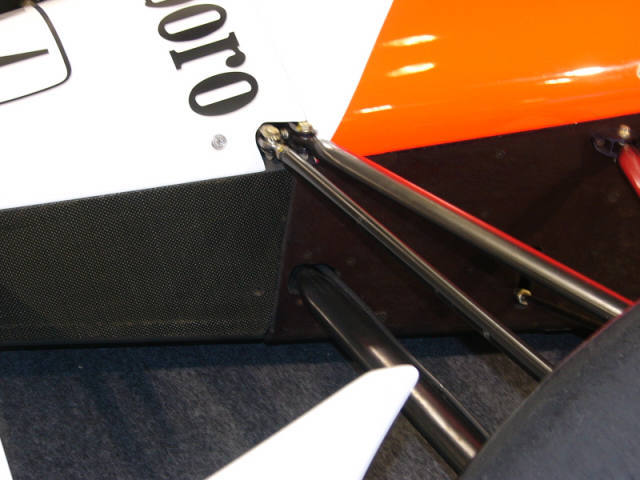
6.ディアゴスティーニ版のボディ・カウルはつなぎ目の位置がおかしいことが判明しました。
7.結果、フロント・サスペンション・アッパー・アームの取り付け位置を変更することなく。
8.ボディ・カウルを改造することで、実車と同じになることが判明。
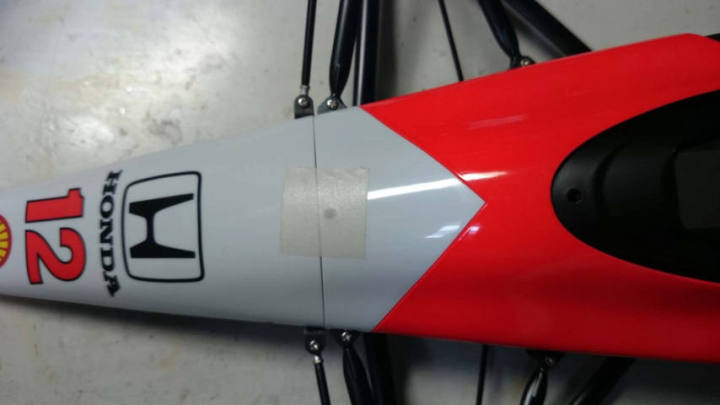
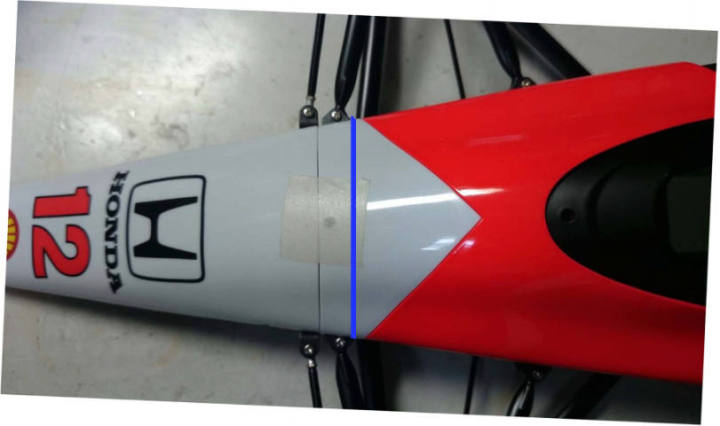
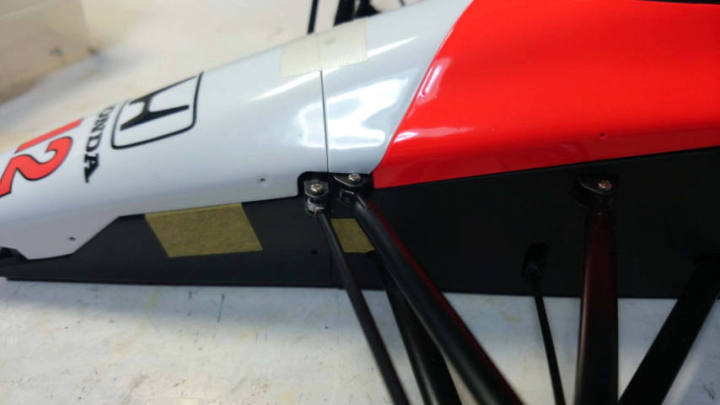
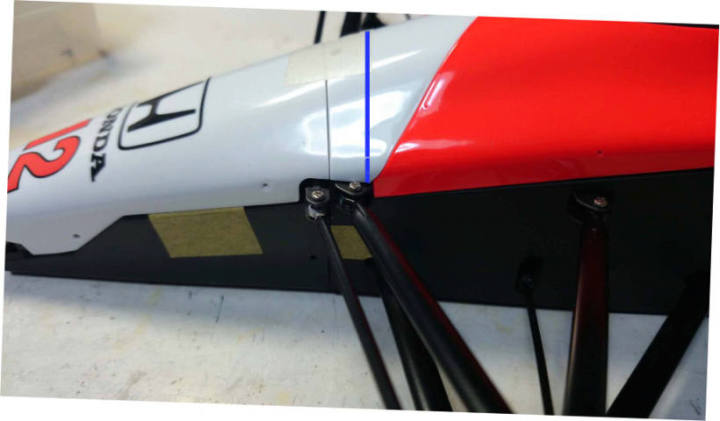
9.フロント・カウルのつなぎ目を写真の青ラインの位置に改造することにしました。
ステアリング・ロッド、自作編(途中経過)
1.ディアゴスティーニ版ステアリング・ロッド用ブラケットは大きすぎます。
2.ステアリング・ロッド自体を自作品に置き換えます。
3.直径 2.0 mm 真鍮パイプを使用します。
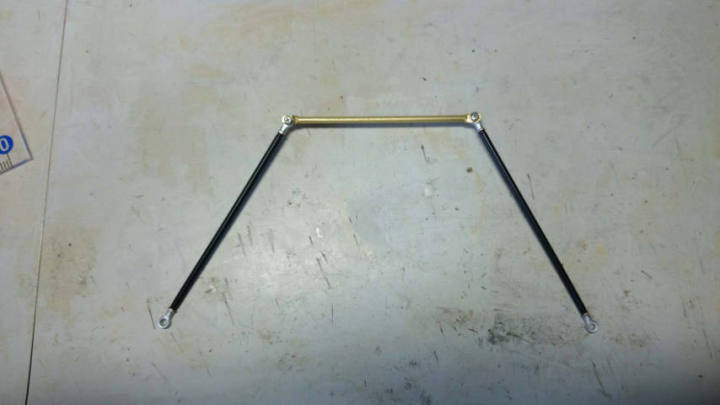
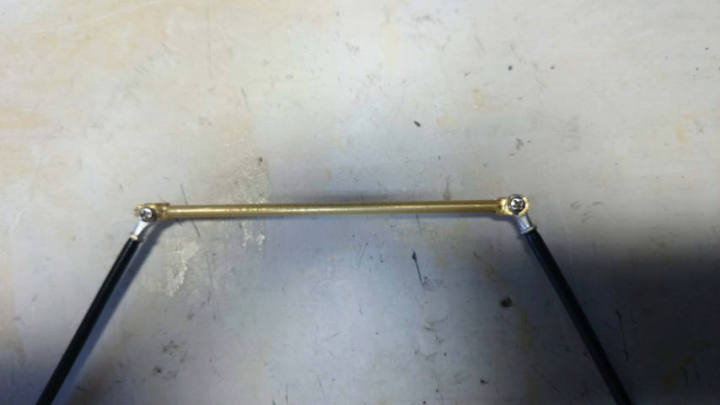
4.ディアゴスティーニ版はプラスチック製で剛性もない。
5.ステアリングとフロント・ホイールの連動は犠牲にします。
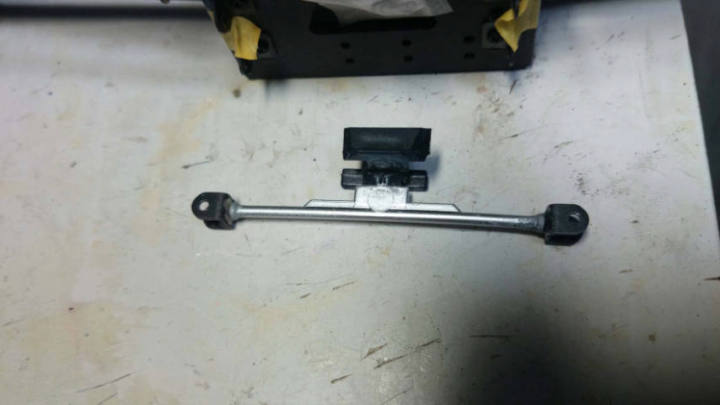
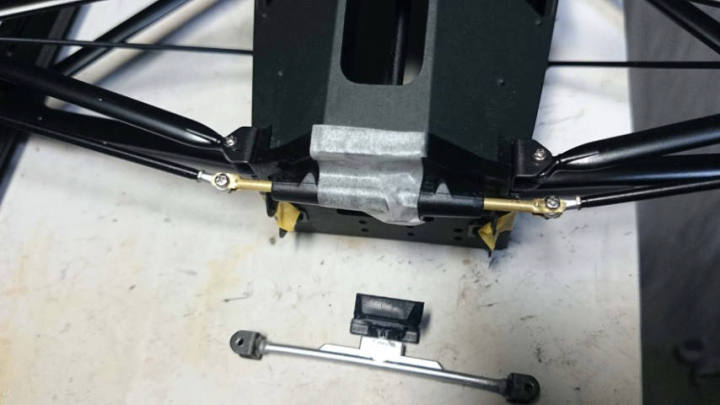
6.細かなディテールは着色時に成型します。
7.あまりにもボロボロだったので再製作しました。
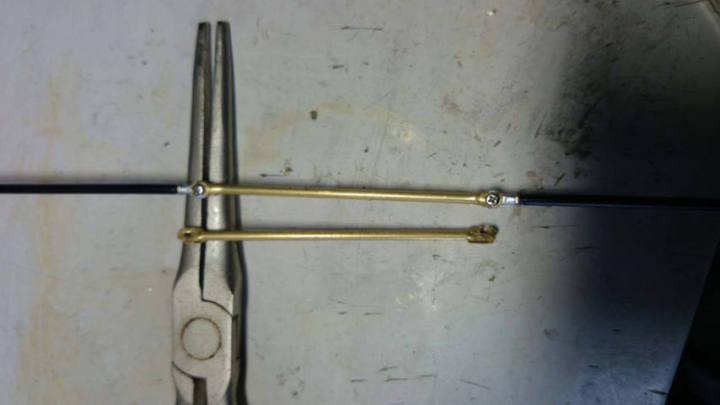
8.アッパー・アーム先端を少し削ったため、ロッドのサイズを短くする必要が出てきました。
9.再製作します。
10.短くしました。
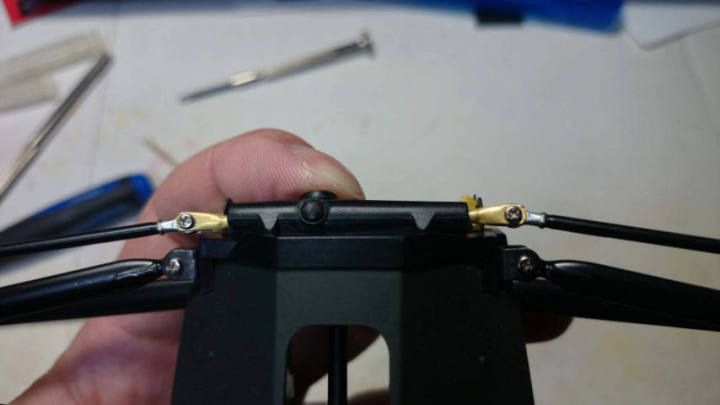
11.逆に短くなりすぎたかな?
12.見た目はかなり良くなったと思います。
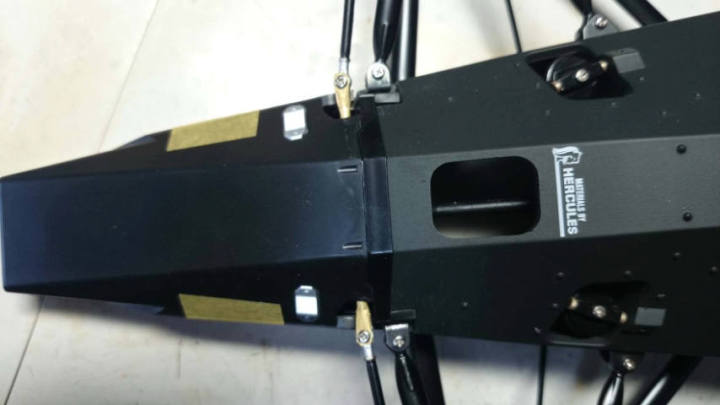
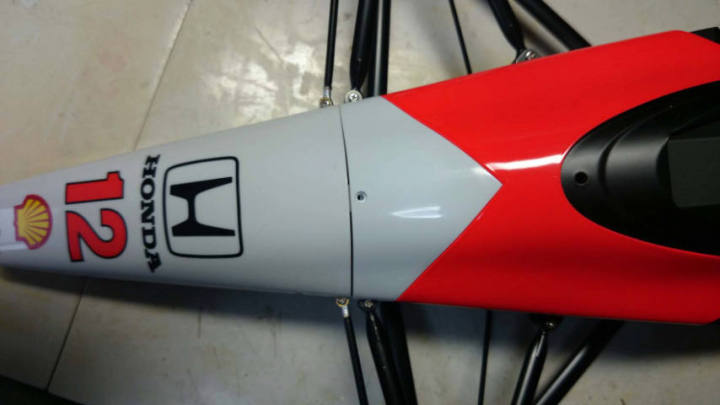
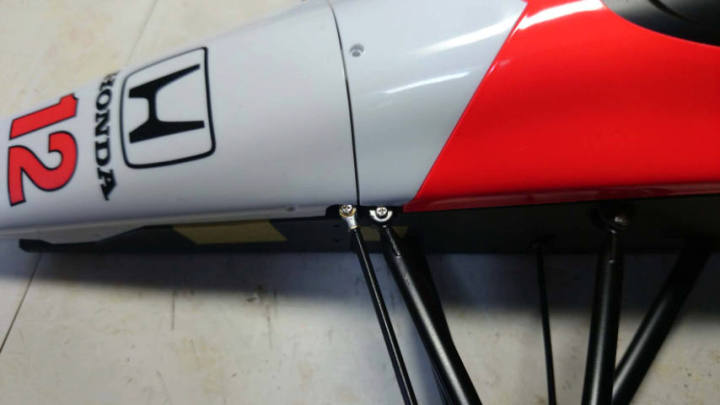
13.4作目、これで「トー」がうまく決まりました。
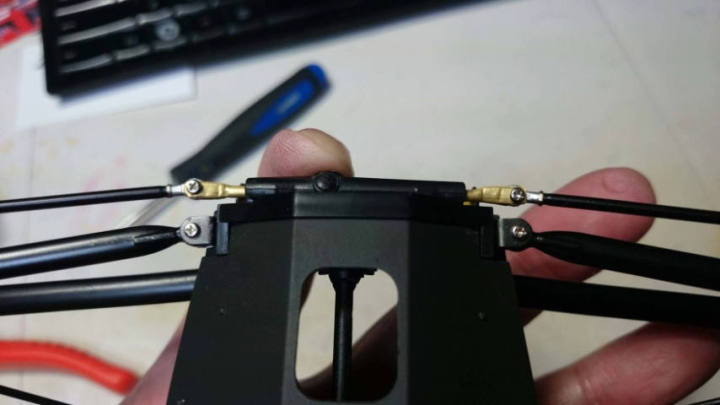
フロント・サスペンション・アッパー・アーム用ブラケット改造編(途中経過)
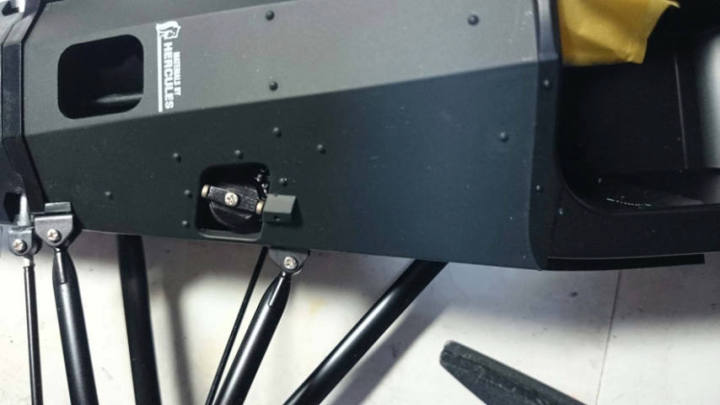
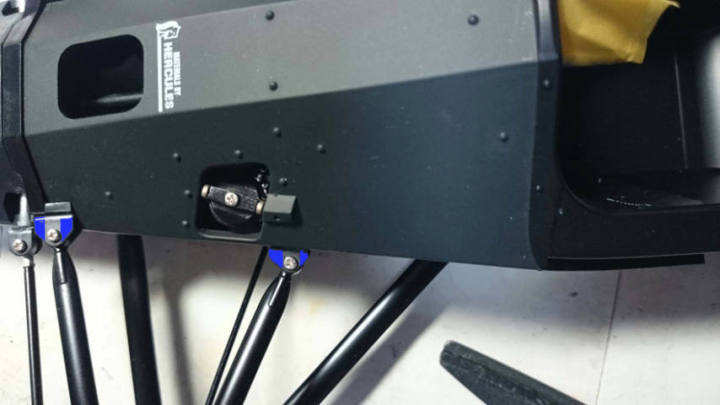
1.フロント・カウルのつなぎ目を変更する前に
2.フロント・サスペンション・アッパー・アーム取り付けブラケット自体の大きさを小さくします。
3.アッパー・アーム取り付けブラケットの後方はそのまま使用します。
4.アッパー・アーム取り付けブラケットの前方はもともとステアリング・ロッド用ブラケットを置き換えました。
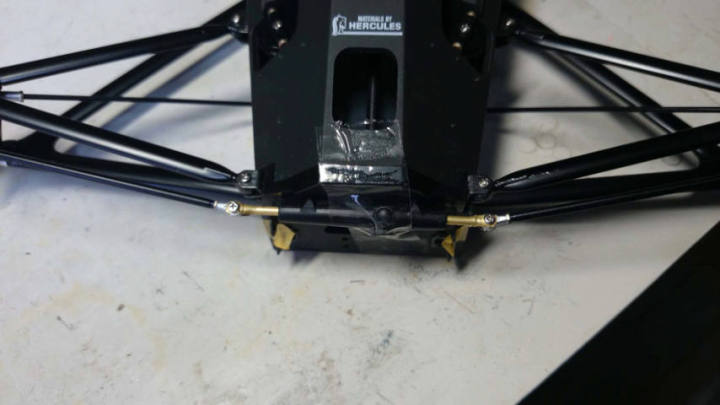
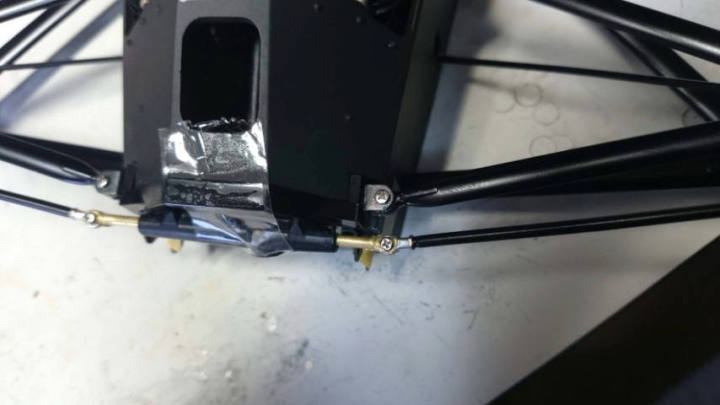
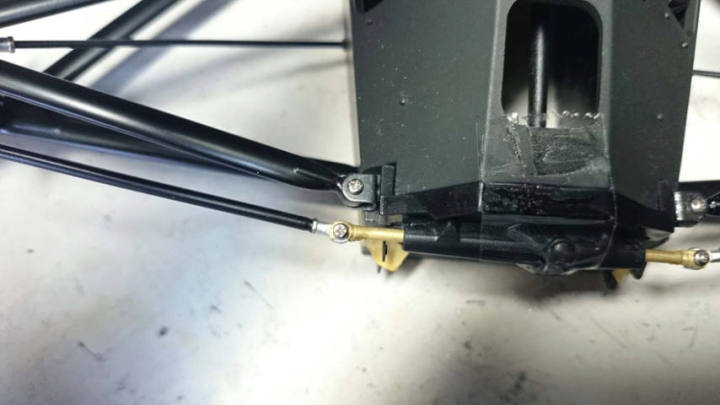
5.ブラケット・サイズが小さくなったため、アッパー・アーム先端を少し削りました。
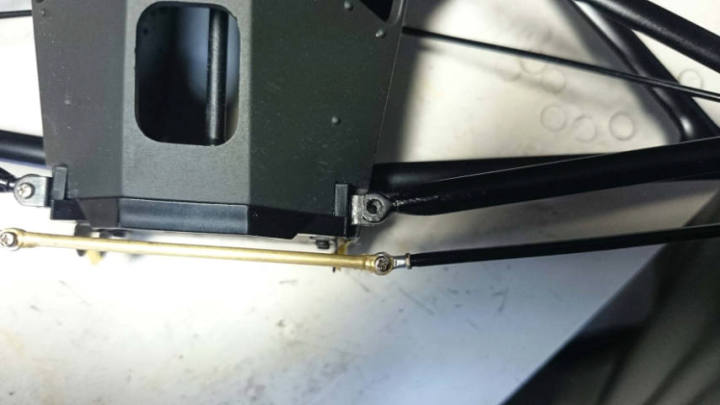
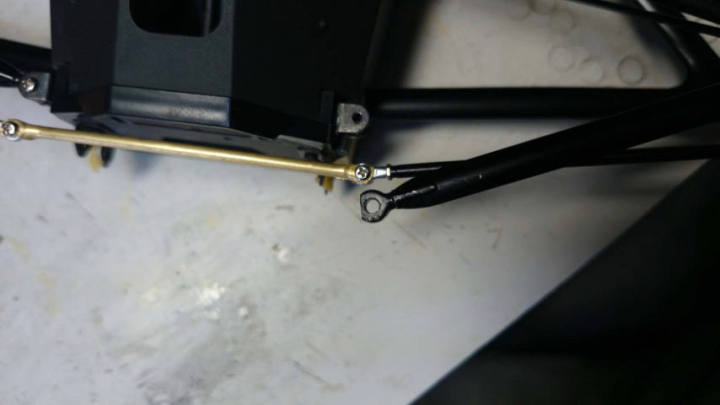
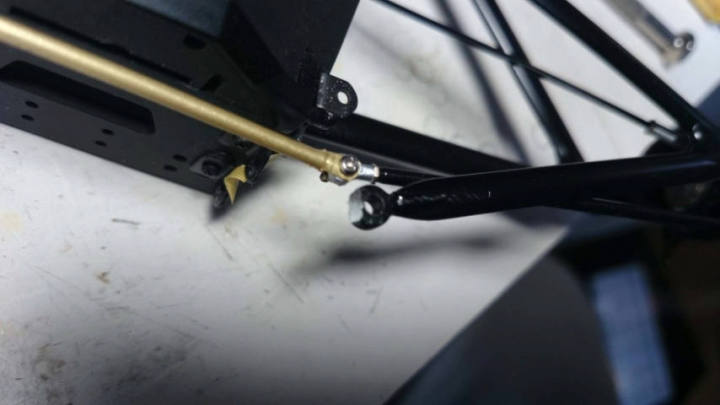
6.ブラケットのサイズが小さくなったためかなり見た目はよくなったと思います。
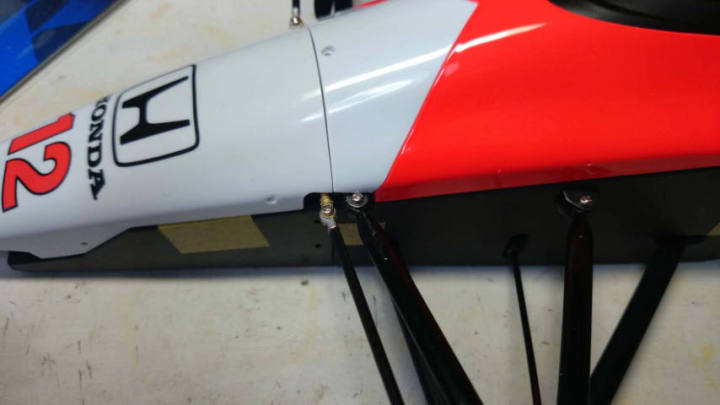
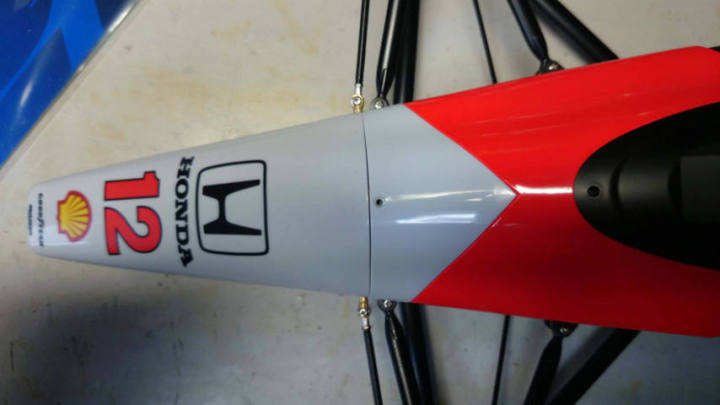
ホイール・ハブ・リング自作編(途中経過)
1.ディアゴスティーニからの回答で、ホイール・ハブ・リングの提供が無いと回答をいただきました。
2.konakiさんのアイデアを真似して自作することにしました。
モノコック・フロント・プレート、ディテールアップ編(途中経過)
1.実車の写真とディアゴスティーニ版を比べると穴の開き方が明らかに違います。
2.タンクはやや大きめですが、デザインは忠実に再現されているようです。
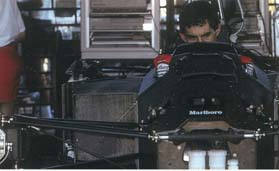
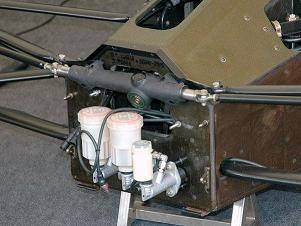
フロント・サスペンション・アッパー・アーム、ディテールアップ編(計画中止)
1.実車の写真と仮組したディアゴスティーニ版のフロント・サスペンションを比べてみる。
2.明らかにデザインが破綻しています。
3.流石に、アマルガム製は忠実に表現されています。
4.一番の問題点はフロント・アッパー・アーム前方取り付け部分の位置が全く違うことです。
5.モデルの方は取り付け用ブラケットが耐久性を考慮して大きすぎます。
6.アマルガム製もフロント・サス・アーム・ブラケット後方部分は比較的大きくなっています。
7.何故?ディアゴスティーニ版のデザインが破綻しているかというと
8.フロント・アッパー・アーム前方ブラケットを専用設計せず、後方用と共用部品にしたことです。
9.その為、取り付け位置が外側、後方にずれてしまっています。
10.ブラケットは自作で対応できますが、フロント・サス・アームの長さが足りなくなり、角度も違います。
11.フロント・サス・アッパー・アームの改造を考えなければいけません。
12.あれからよく実車の写真を観察しました。
13.すると、フロント・サス・アッパー・アーム後方の取り付け位置が違うことが発見できました。
14.つまり、フロント・サス・アッパー・アームは全体的に後方に取り付けられているのです。
15.ということで、フロント・サス・アッパー・アームは改造せず、前後のブラケット位置を前方にずらす。
16.ブラケットの自作で対応の可能性が出てきました。
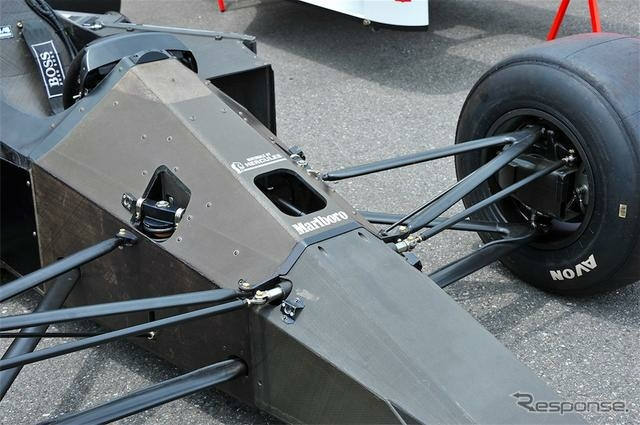
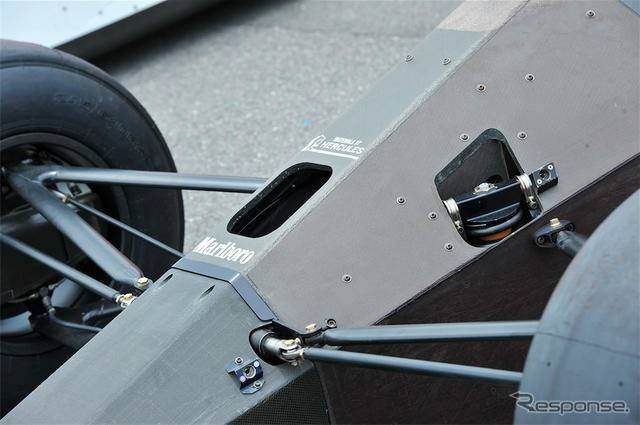
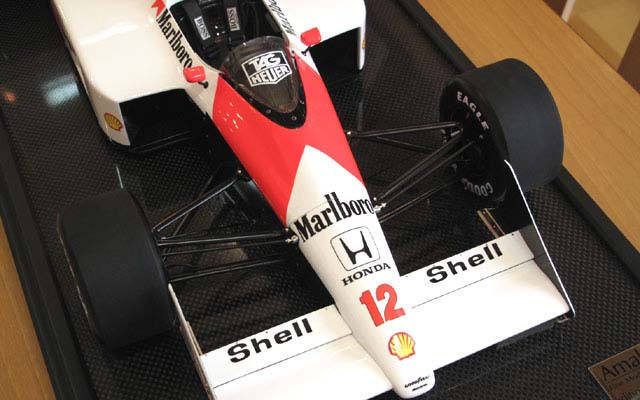
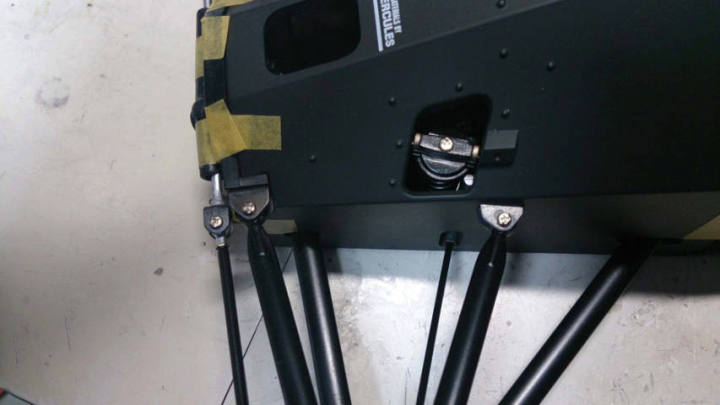
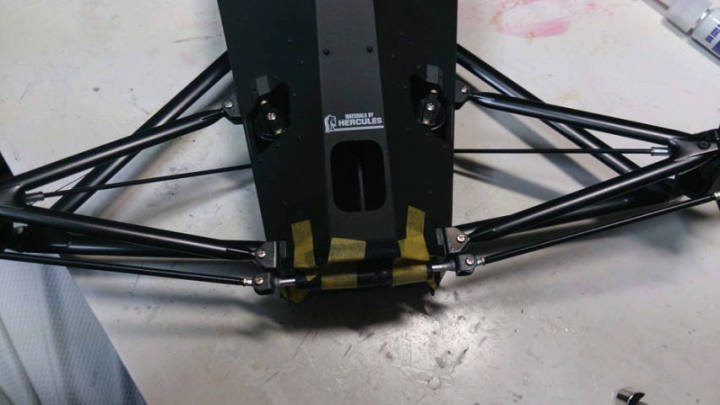
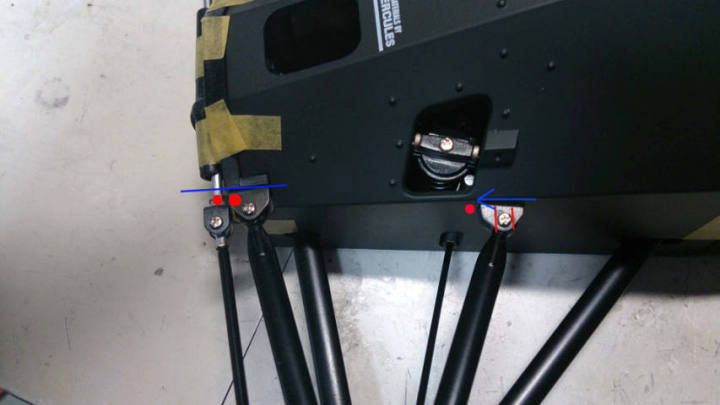
17.ブラケットを外して検証してみました。
18.やはり、フロント・サス・アッパー・アームの改造は必須ですね。
19.フロント・サス・アッパー・アームの改造について、角度の変更は難しいので諦めます。
20.長さの変更については挑戦してみます。
21.フロント・サス・アッパー・アームの改造が成功すれば、計画実行。
22.フロント・サス・アッパー・アームの改造が失敗すれば、この計画諦めます。
23.モノコック・フロント・エンド・プレートの位置も全然おかしい位置にあります。
24.モノコック・フロント・エンド・プレートというより、フロント・サス・アッパー・アームのブラケットでしょう。
25.フロント・サス・アッパー・アームのブラケットは自作します。
26.モノコック・フロント・エンド・プレートを取り付ける部分はパテ埋めですね。
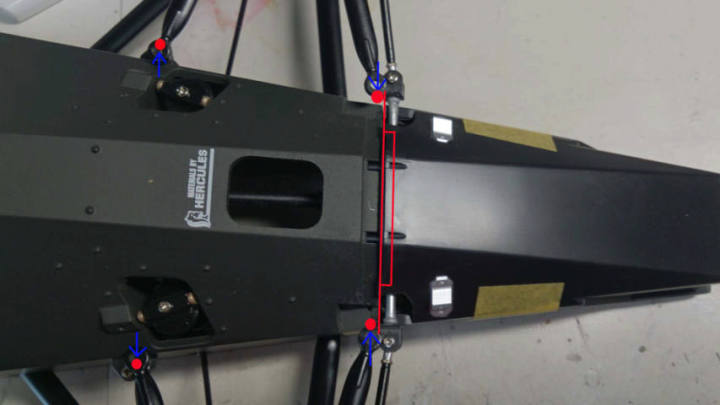
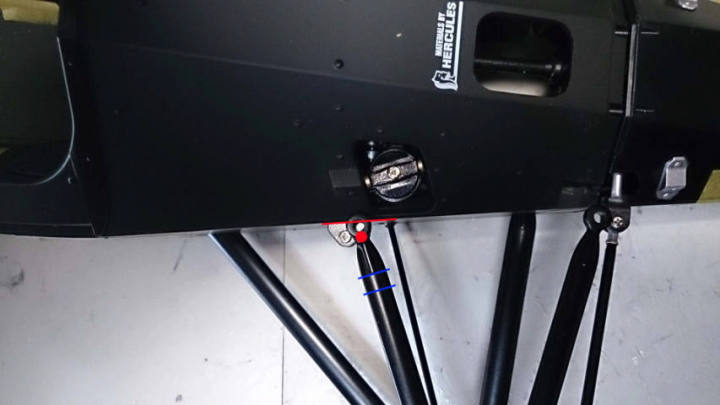

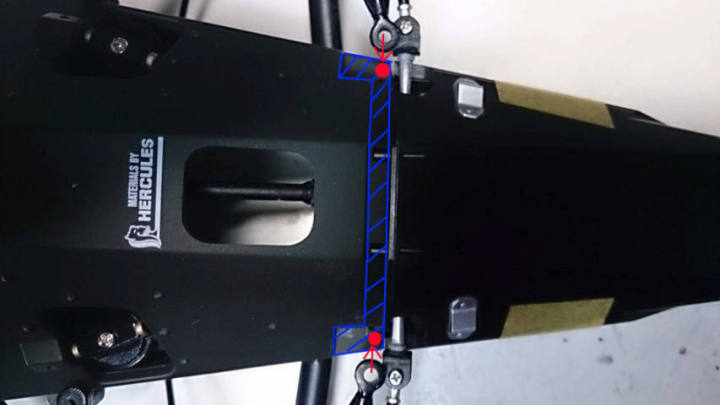
27.フロント・サス・アッパー・アームのブラケットとモノコック・フロント・エンド・プレートを試作しました。
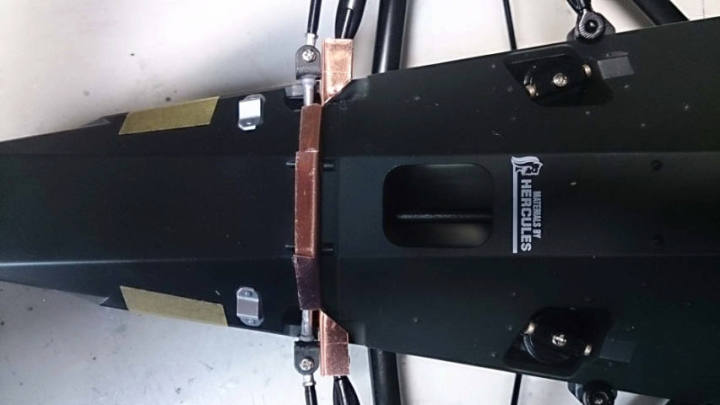
28.フロント・サス・アッパー・アーム全体が前方へずれます。
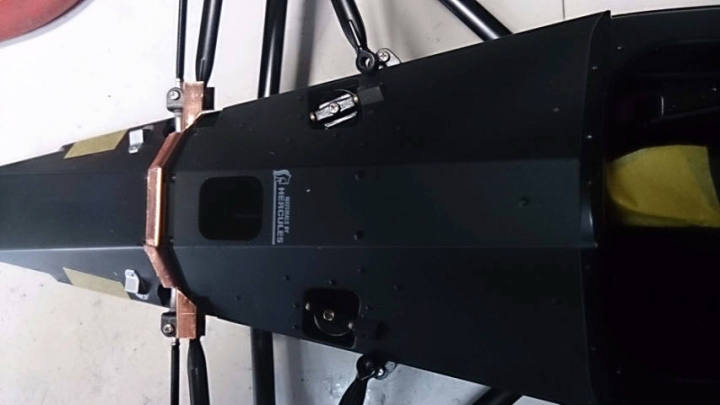
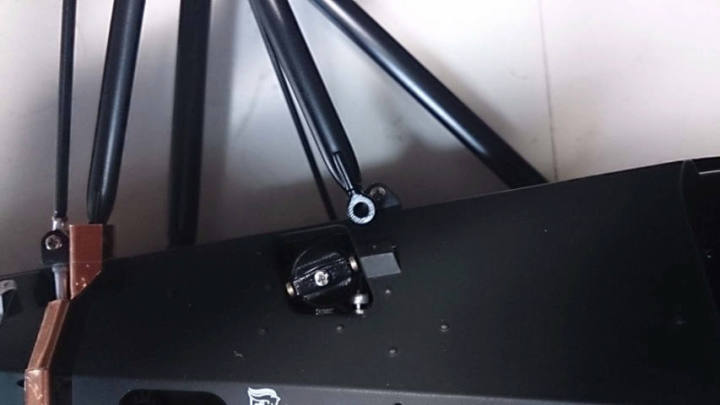
29.フロント・サス・アッパー・アーム後部のブラケットを試作しました。
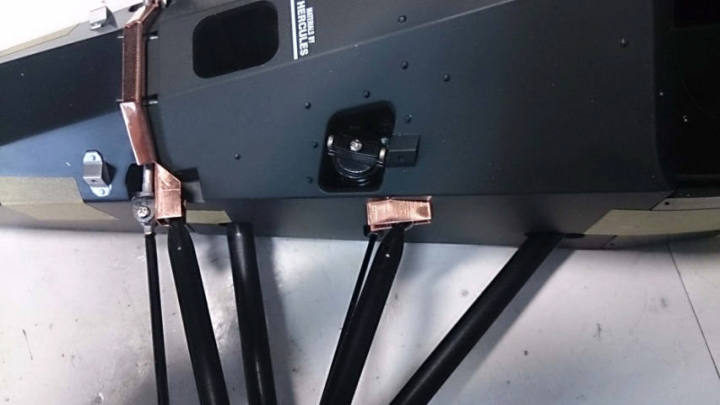
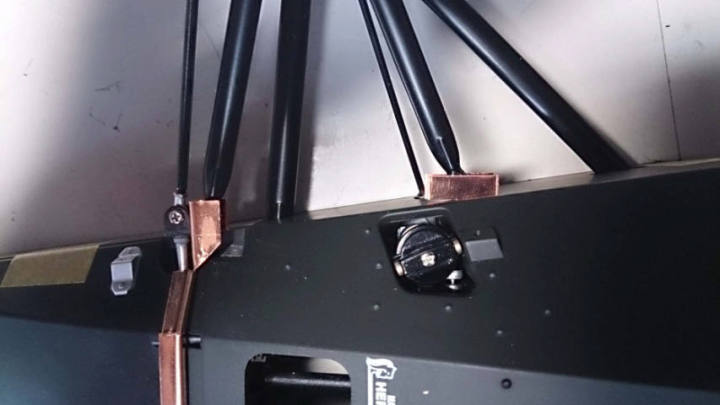
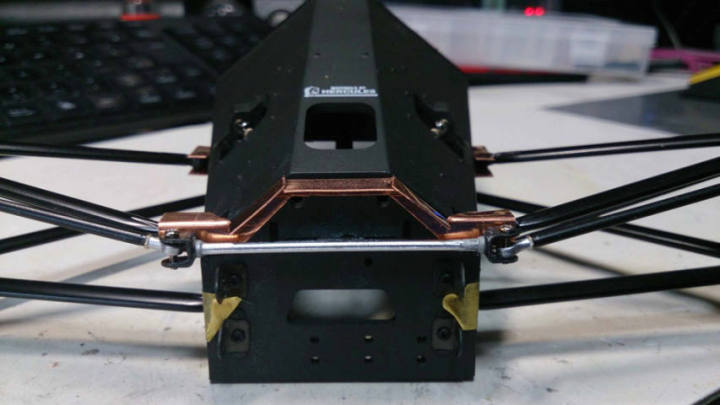
30.フロント・サス・アッパー・アーム前方は本来であれば車体の上に位置します。
31.現時点ではアームを伸ばしていない為、ブラケットの方を延長しています。
32.フロント・サス・アッパー・アームの後部アームの短縮は行いません。
33.前方のアームを延長するかブラケットを延長するかは、様子を見ます。
34.銅で試作した。ブラケットは半だ付け、リュウーターで削り、形を整えます。
35.あれから沢山の写真を見て間違いを見つけました。
36.フロント・サス・アッパー・アーム前方のブラケットは車体より外側に出ていました。
37.以下の写真の赤丸印は間違いです。
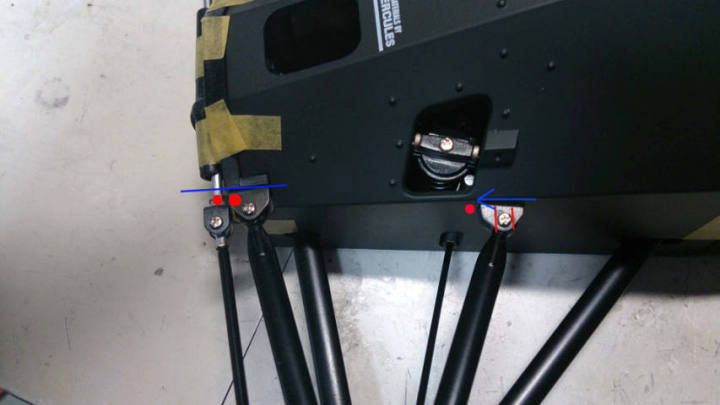
38.よって、前方のアームを延長する必要がなくなりました。
39.これで、改造作業がかなり楽になりました。
40.ところが、ディアゴスティーニのデザインの破綻をもう一つ発見しました。
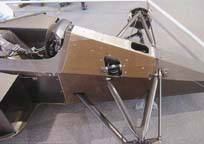
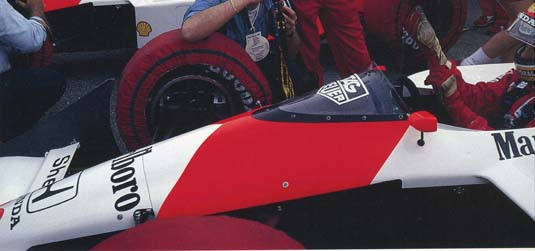
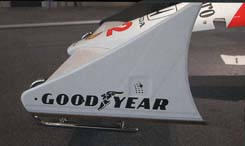
41.ディアゴスティーニ版のボディ・カウルの先端部分、つまりノーズ・カウルと繋がる部分です。
42.ディアゴスティーニ版のボディ・カウルの先端部分にはブラケット用の切り欠きが存在します。
43.ところが、実車のボディ・カウルの先端部分にはブラケット用の切り欠きがありません。
44.このデザインの破綻がなぜ起こったかはもうここでは触れません。
45.モノコック・フロント・エンド・プレートを取り付ける位置が、上部と下部で矛盾が生じています。
46.改造はこの矛盾点をどの様に修正するかですね。
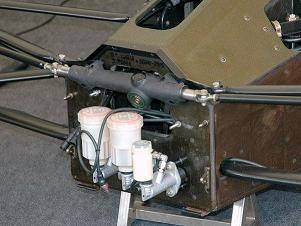
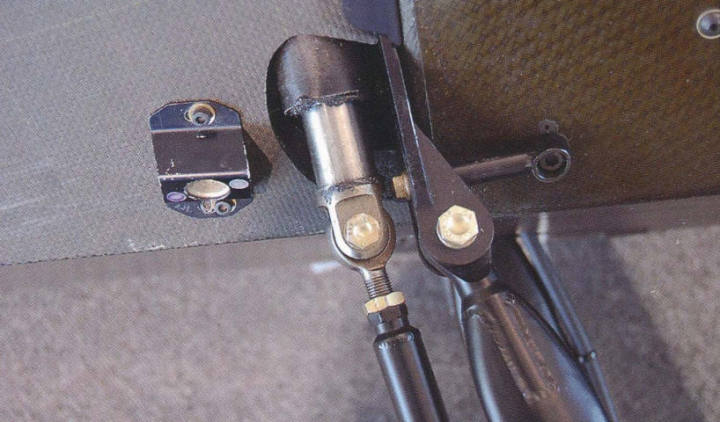
47.この写真を参考にして、ノーズコーンをガイドする部分とアッパー・アーム前方取り付け用ブラケットを試作してみます。
48.設計図 PDF
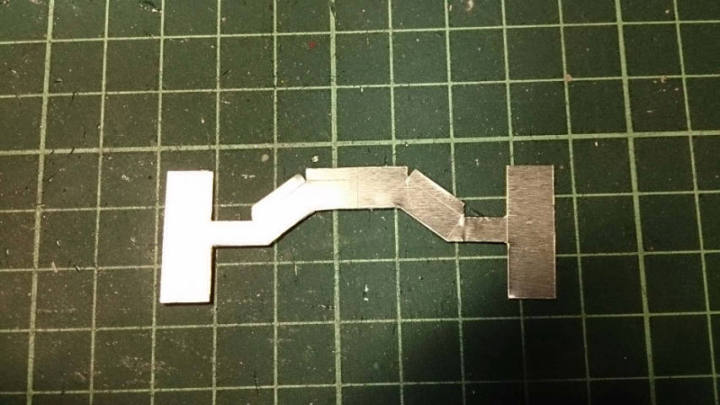
49. 0.3mm アルミ板で試作。
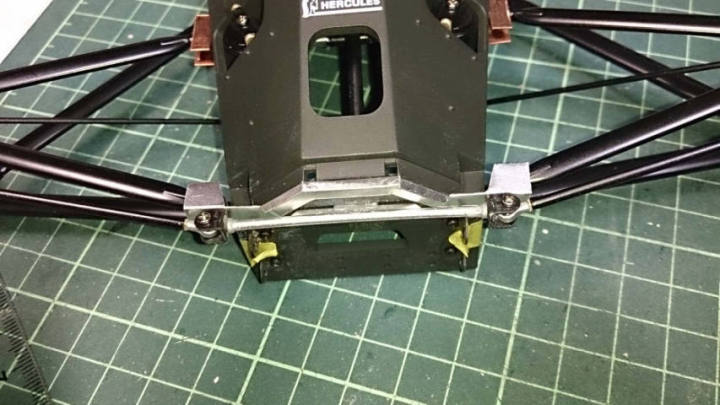
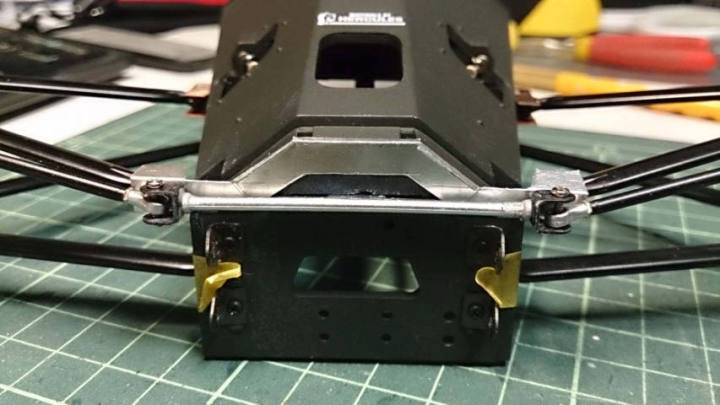
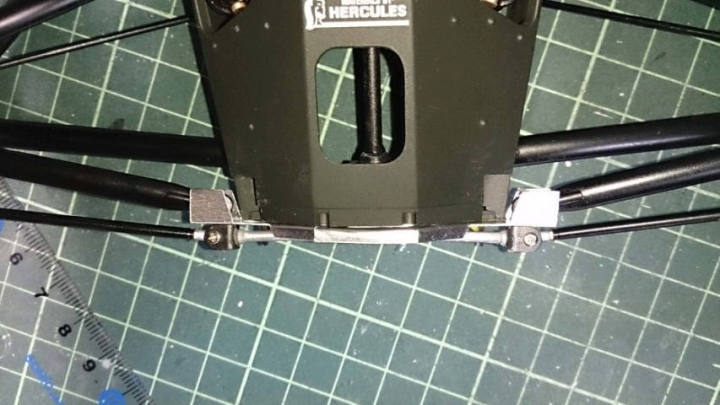
50.サイズ合わせ。
51.アルミ板は加工しやすいが、耐久性に欠ける。
52.銅板を使用すれば、加工がしにくいが耐久性はある。
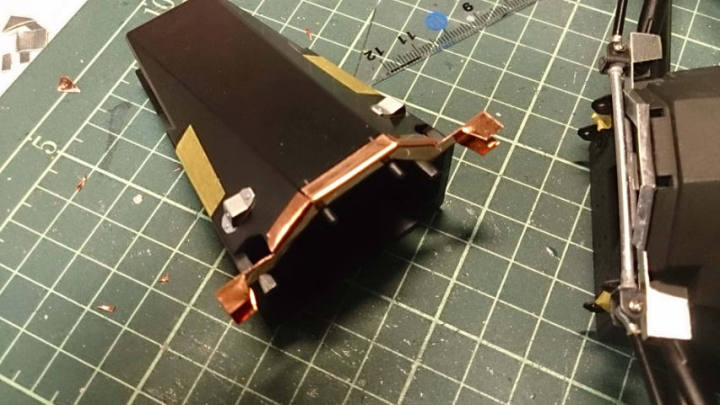
53.銅板をリューターで成形し、半だ付け等で補強できる。
ステアリング・ロッド、ディテールアップ編(計画中止)
1.実車の写真と仮組したディアゴスティーニ版のステアリング・ロッドを比べてみる。
2.明らかにデザインが破綻しています。
3.流石に、アマルガム製は忠実に表現されています。
4.一番の問題点はステアリング・ロッド取り付け部分の位置が全く違うことです。
5.モデルの方は取り付け用ブラケットが耐久性を考慮して大きすぎます。
6.何故?ディアゴスティーニ版のデザインが破綻しているかというとステアリングと連動させているからです。
7.ブラケットが大きすぎ、ステアリング・ラックが左右に動くとき内側に入らない為、位置が外側になっています。
8.ステアリング・ラックを自作します。(ステアリング連動については?)
9.ステアリング・ロッドを長く伸ばす改造をします。
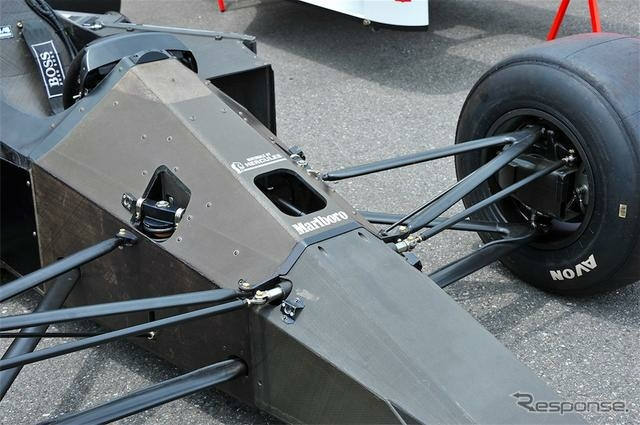
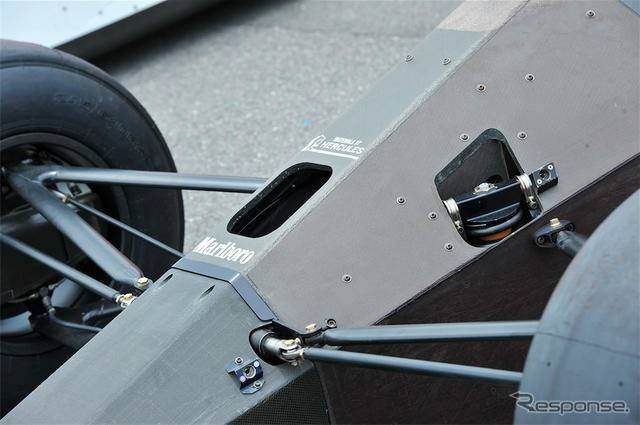
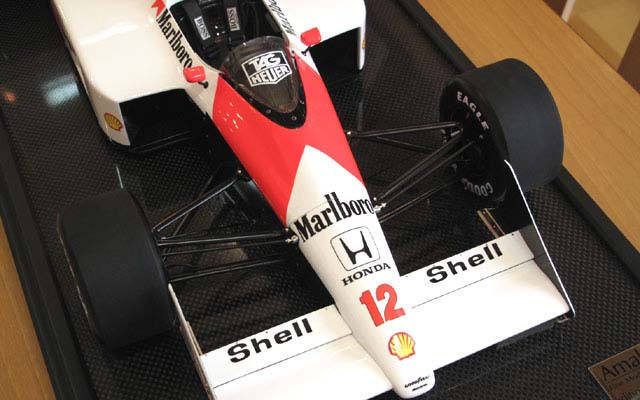
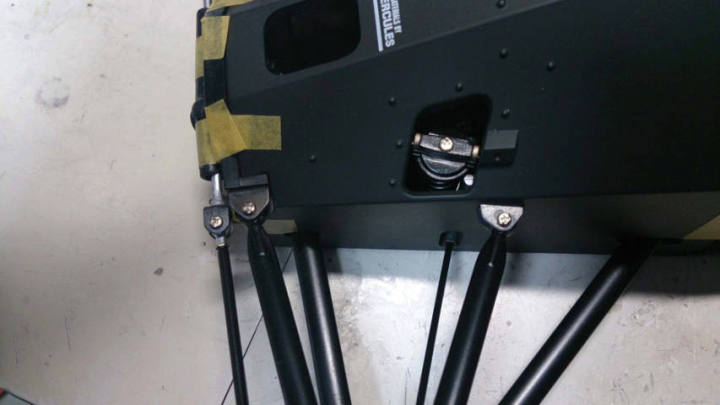
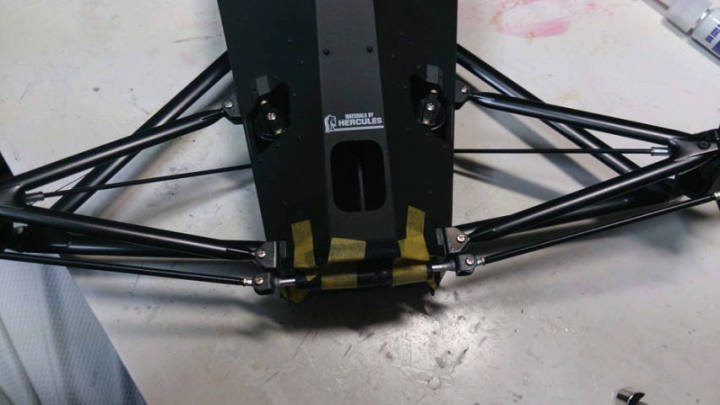
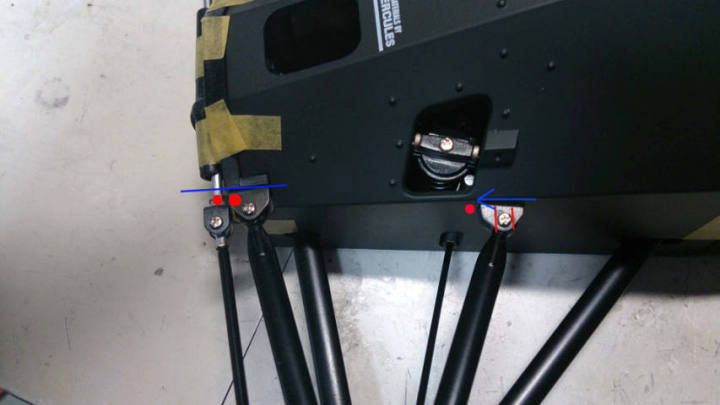
ゴミ防止網、ディテールアップ編途中経過
1.実車の写真を見る限り、おそらく金属製であることは想像できますがかなり柔らかいものでできているようです。
2.ディアゴスティーニ版は厚めの枠がありますが、必要ないように思えます。
3.問題は穴の加工ですね。
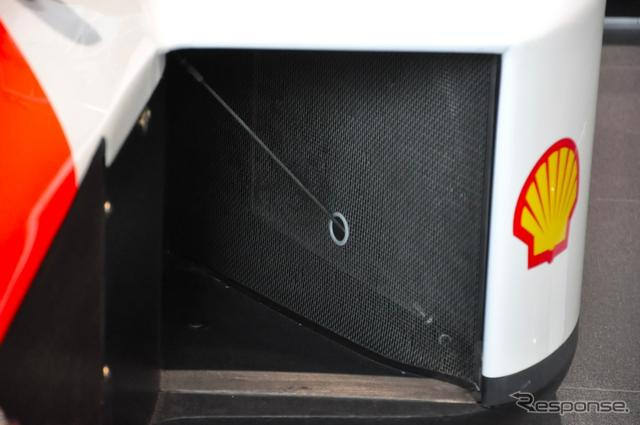
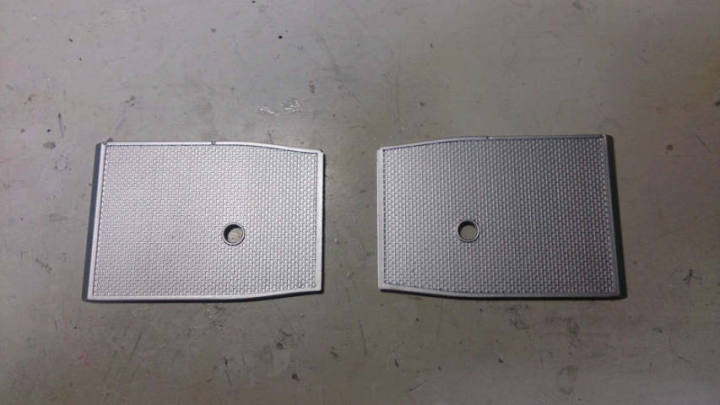
4.ステンレス網を使用しました。
5.穴の大きさは直径 5mm です。
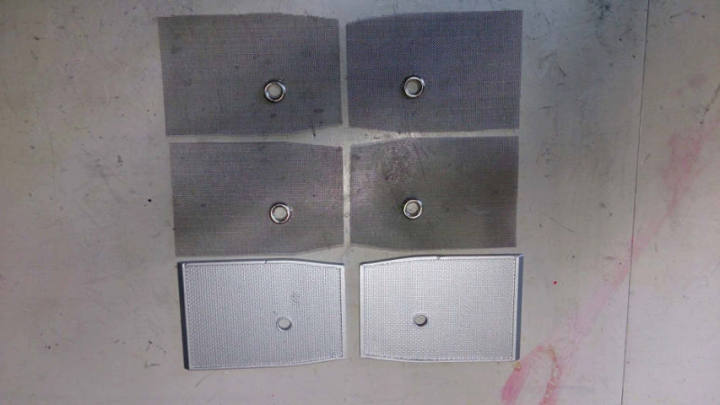
6.穴の大きさがもう少し小さく物がないか物色中。
インター・クーラー、ディテールアップ編途中経過
1.実車の写真を見てもらえればわかりますが、ディアゴスティーにのコアは全く違います。
2.このインター・クーラーはレース・カー専用のインター・クーラーで、高圧縮、強冷却を両立したものです。
3.一般車で採用されないのは高速走行時のみ高性能が発揮できる設計だからです。
4.昔、HKS でドラッグ専用で発売されていました。
5.ラジエータのディテールアップで採用した方法を応用します。
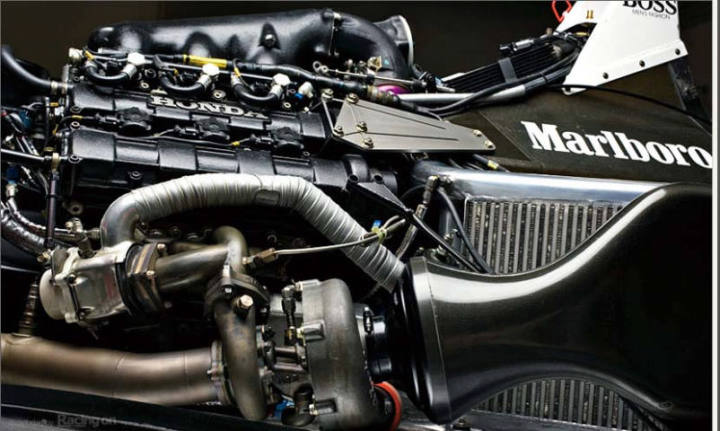
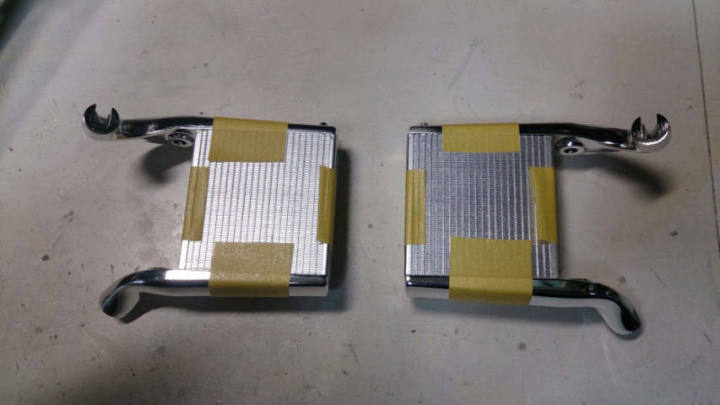
6. 0.1mm 厚アルミ板をラジエータのコア製作に使用した GEARBOX で折り目を付けます。
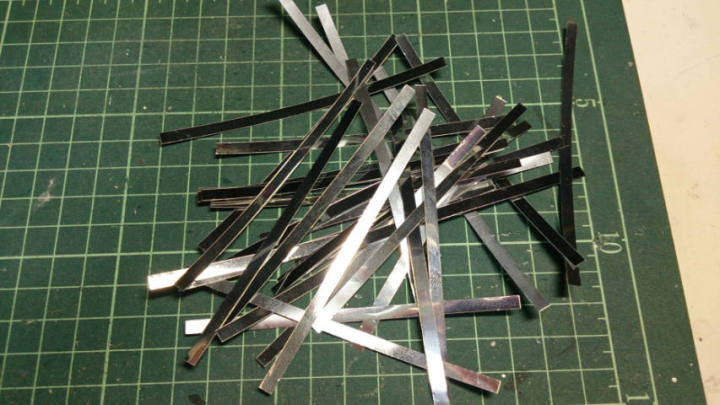

7.ピンセットを使用して折り目を整えます。
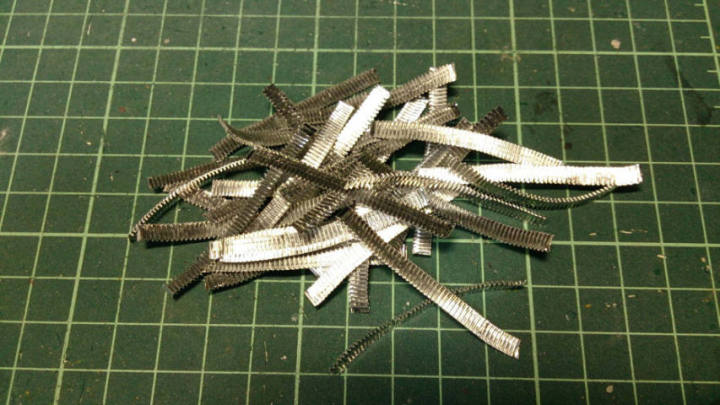
8. 0.3mm 厚のアルミ板、0.5mm 厚アルミ板を準備します。
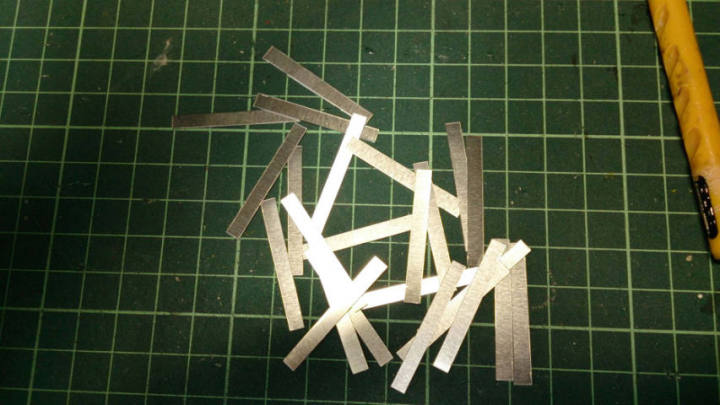
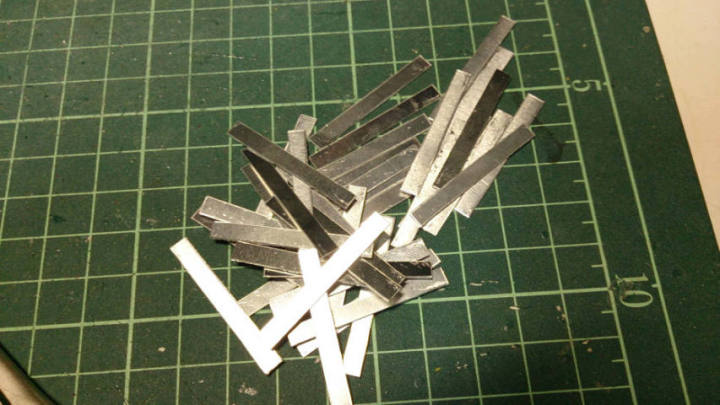
9. 0.3 mm 厚アルミ板と 0.1 mm 厚アルミ板をエポキシ接着剤で接着します。
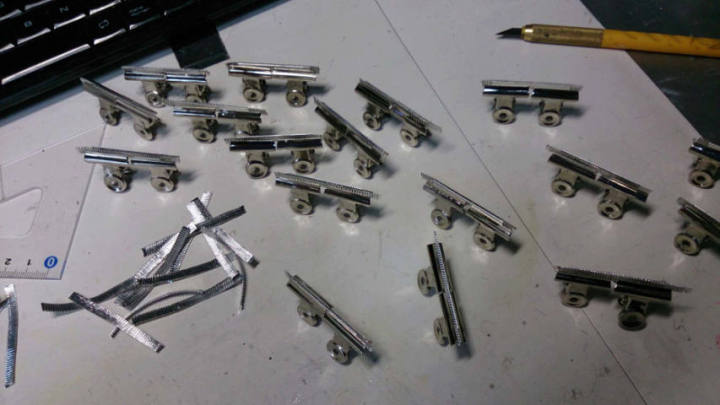
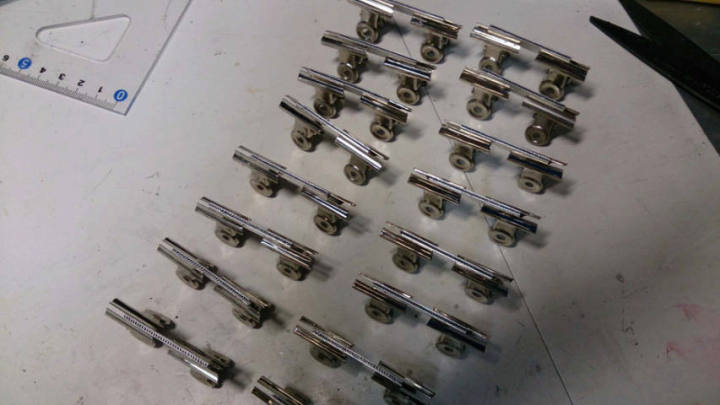
10.出来上がりコアの間に 0.5mm 厚アルミ板を挟み込み、接着していきます。
11.インター・クーラーの場合、コアの奥に光が入らないので、四角アルミ板の上に張り付けました。
12.固定した後、表面を削りました。
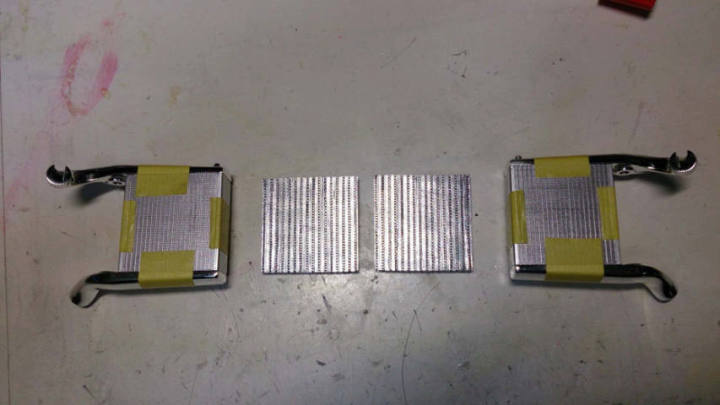
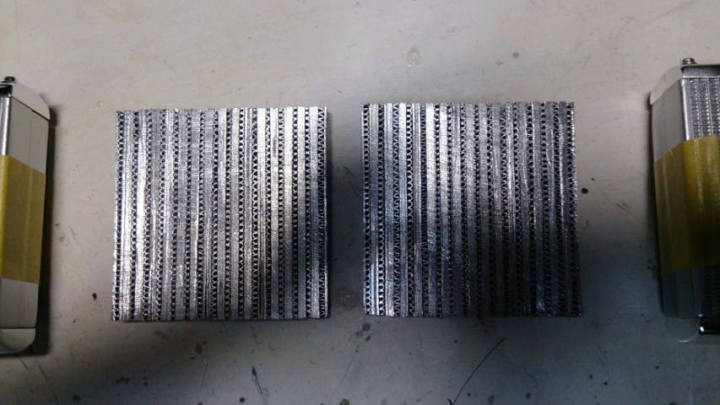
13.サイド・パネルを取り付け、試作品 1 号が完成しました。
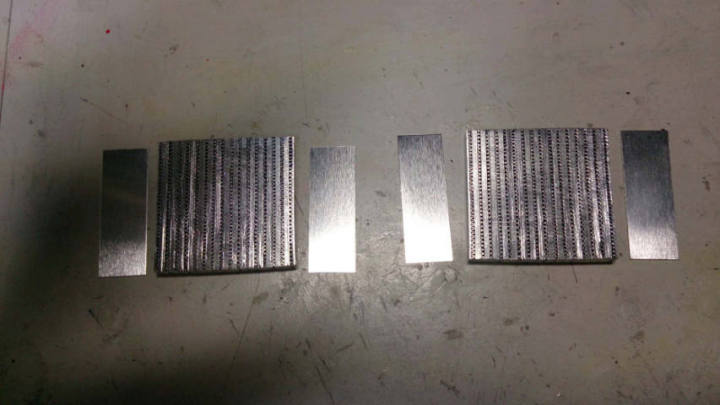
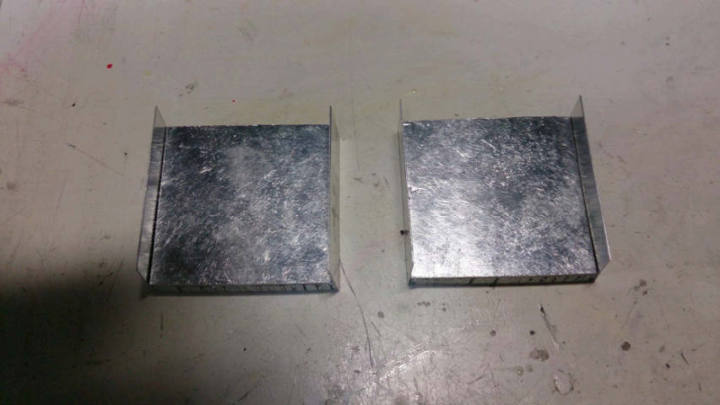
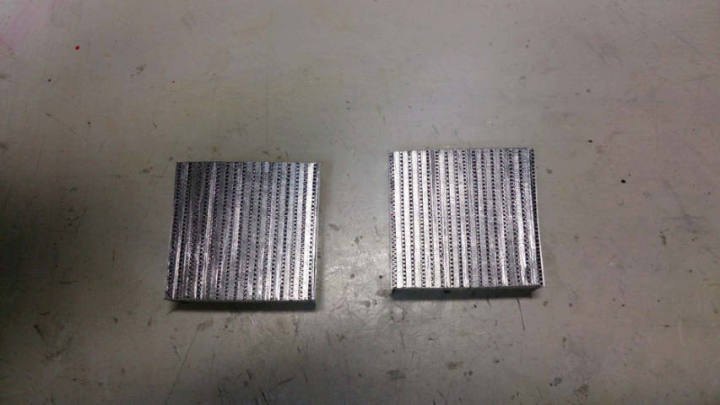
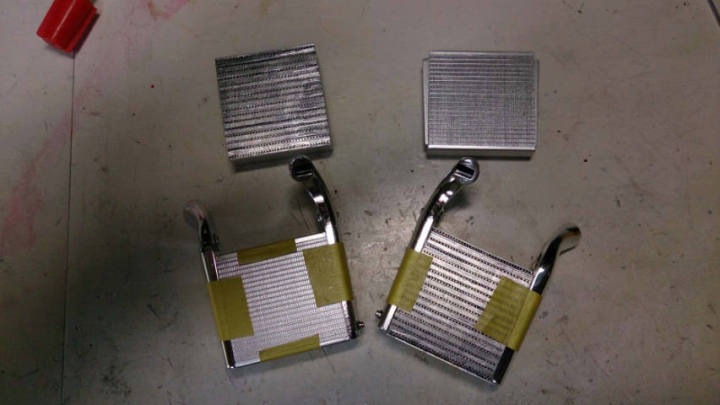

14.製作途中、もう一つのアイデアが浮かんだので試作品 2 号を製作します。
15.同じように 0.1mm 厚アルミ板でコアを製作します。
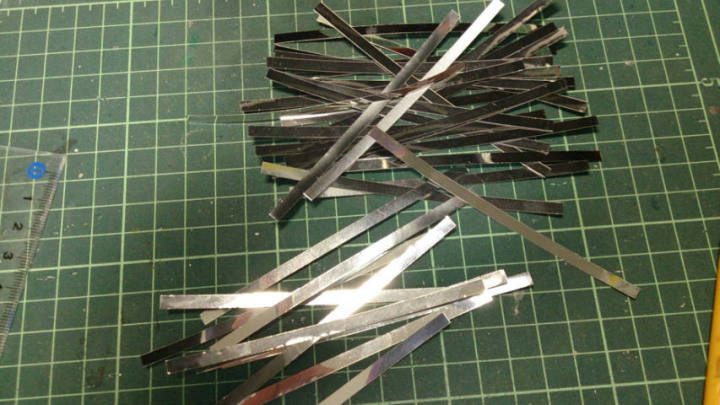
16.圧縮空気の通り道が太いので、 1.0mm 厚アルミ板を使用しました。
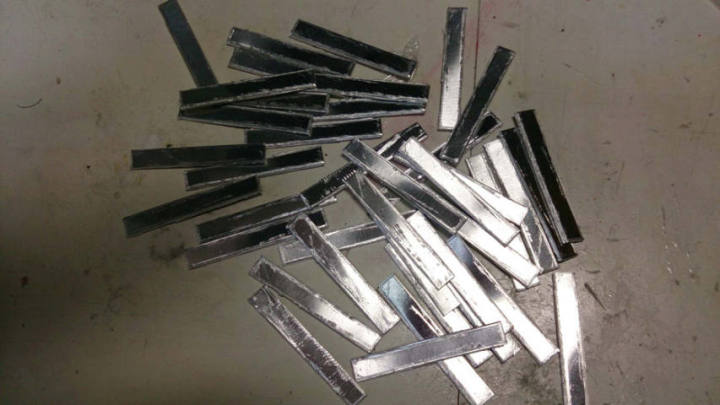
17.試作第 1 号はコアとアルミ板の段差がなかったので、今回は段差を付けてみました。
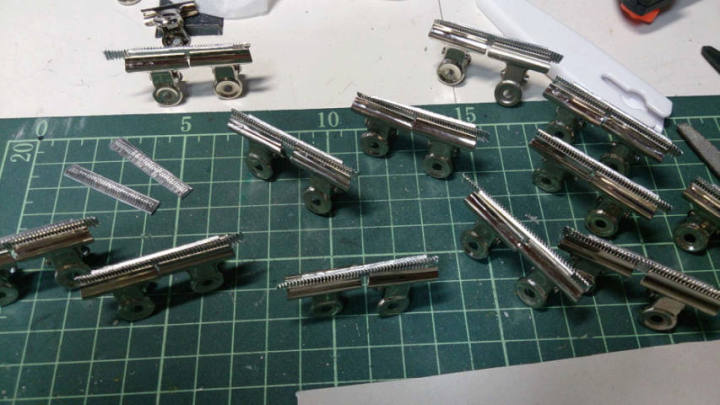
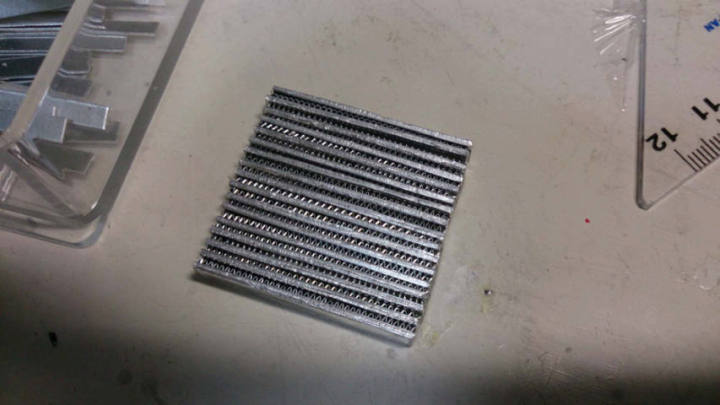
18.表面を削って整えました。
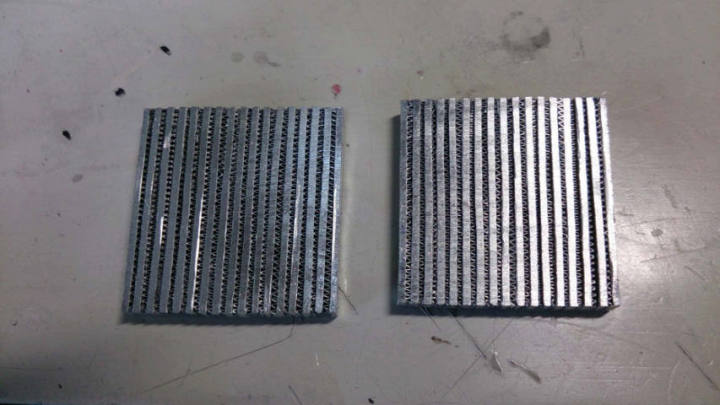
19.あとは、試作第 1 号と同じです。
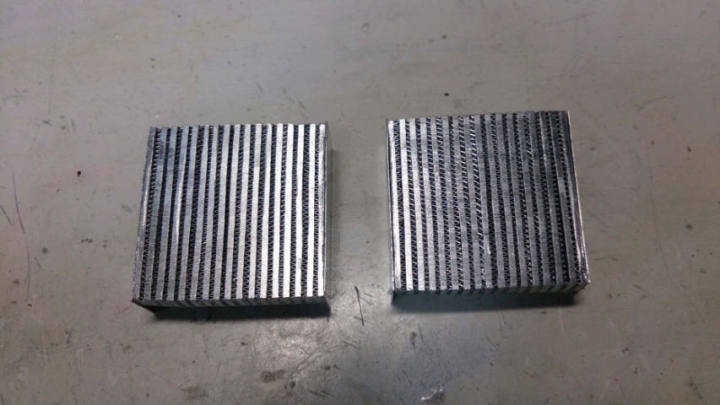
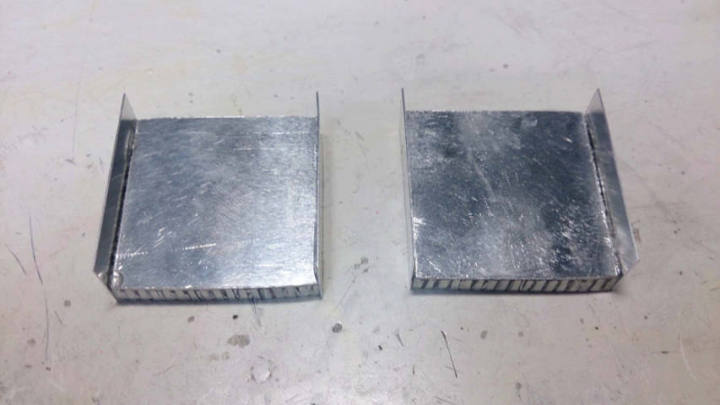
20.実車のコアの積層数と比べると、圧倒的に少ないですが試作第 2 号の出来が良いようです。
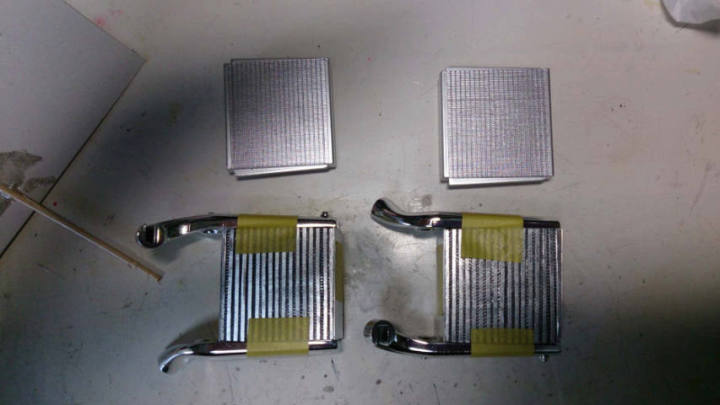
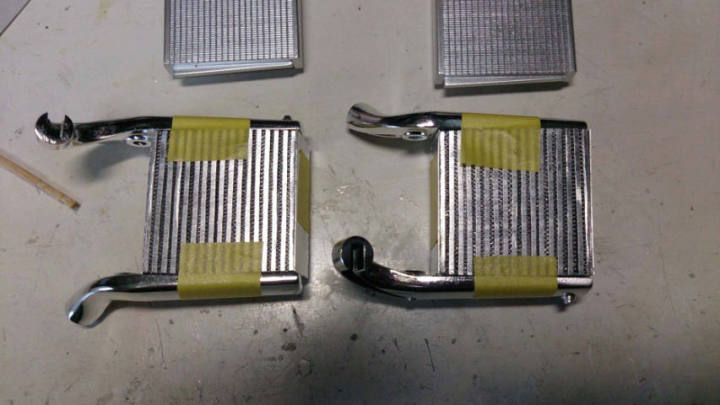
21.インターくーら全体としては製作途中です。
ラジエータ、ディテールアップ編途中経過
1.teruさんのアイデアをパクらせてもらって、ラジエータのディテールアップ奮闘編です。
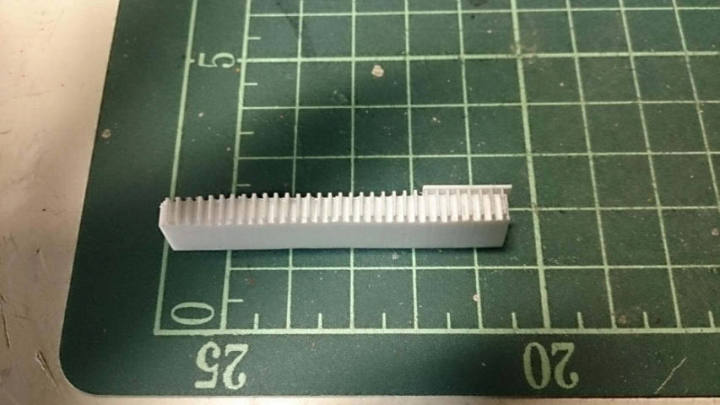
2. 0.5 mm、1.0 mm、0.5 mm、1.0 mm、の治具をプラ版で製作しました。
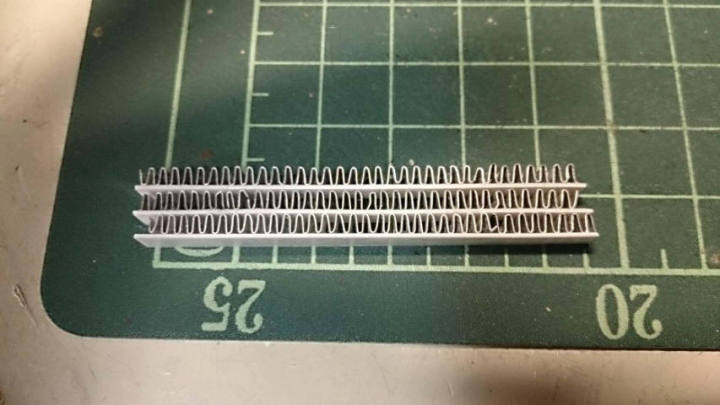
3.厚さ 0.1 mm アルミ板を使用して試作しました。全くの駄作でした。
4.この時点で、アルミ板に均等に折り目を付けないと先に進まないことを理解し、ひたすら歯車探しです。
5.いくつか作ってみましたが、やっぱりおかしい。
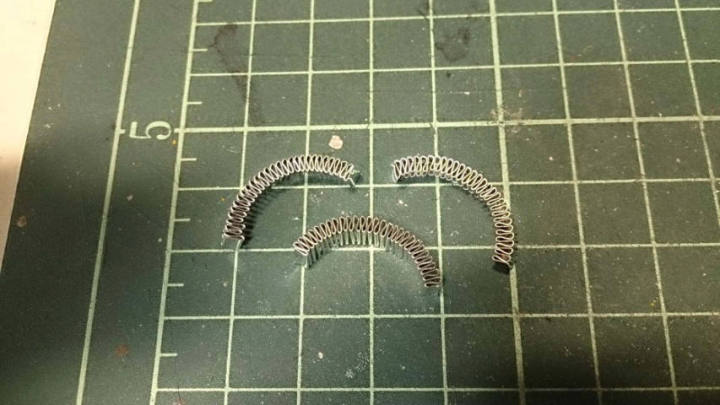
6.ここで、せっかく製作したものを潰してみました。これが結構いけると思い、この方法で進めてみました。
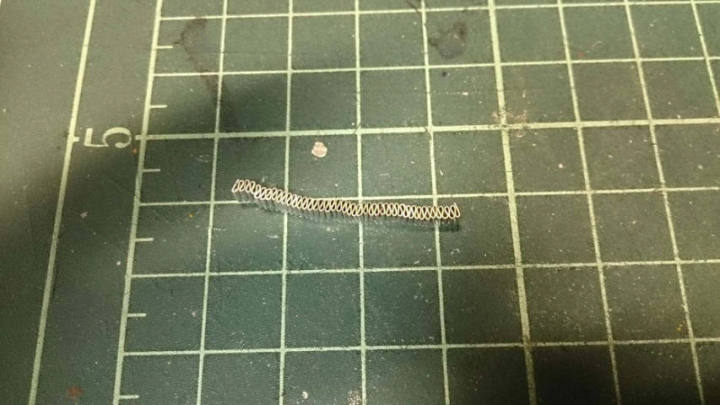
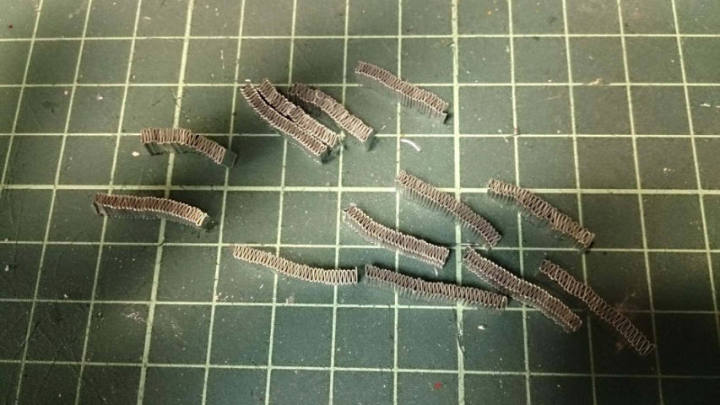
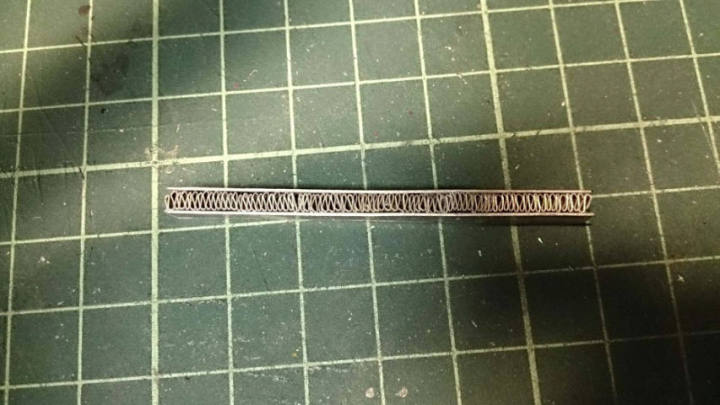
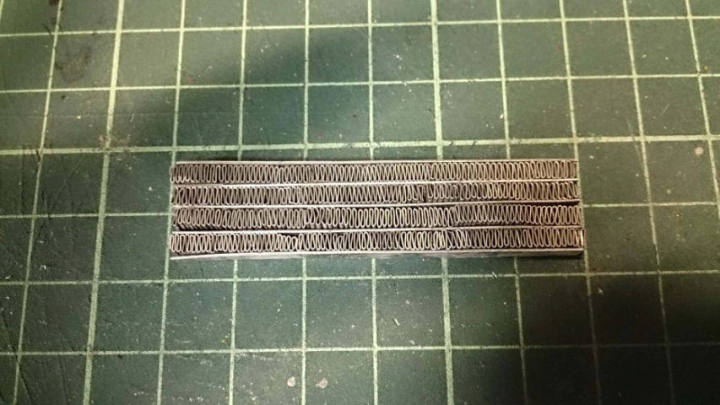
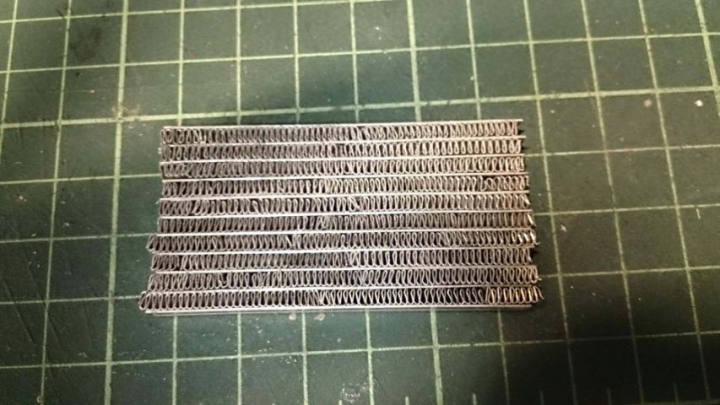
7.ここまで作ってみましたが、あまりにも雑すぎて、製作に時間がかかりすぎて、時間がかかった割には出来が良くない。この時点では諦めました。
8. アルミ板の厚さが 0.1 mm だと汚くつぶれてしまうので、 0.2 mm のアルミ板使って試作しました。
9.これを、うまいこと整形すれば何とかなるかも・・・。
10.とりあえず、これだけのフィンセットを製作しました。これを、うまいこと整形すれば何とかなるかも・・・。
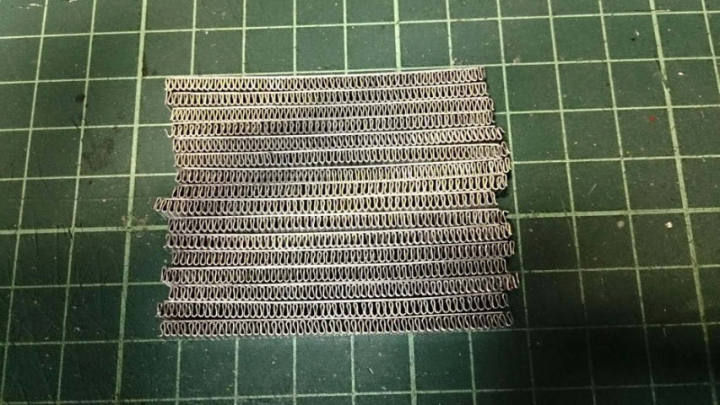
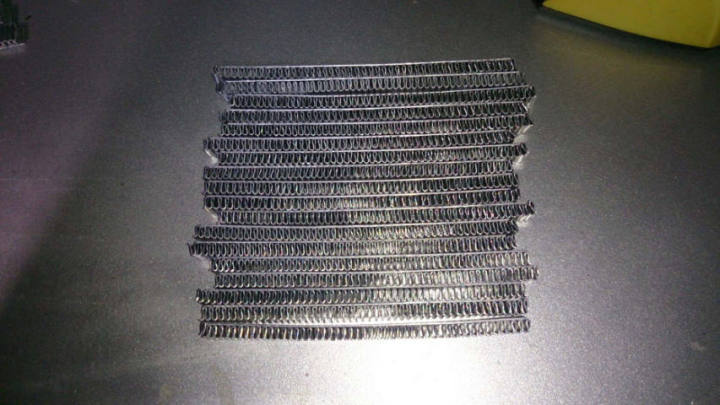
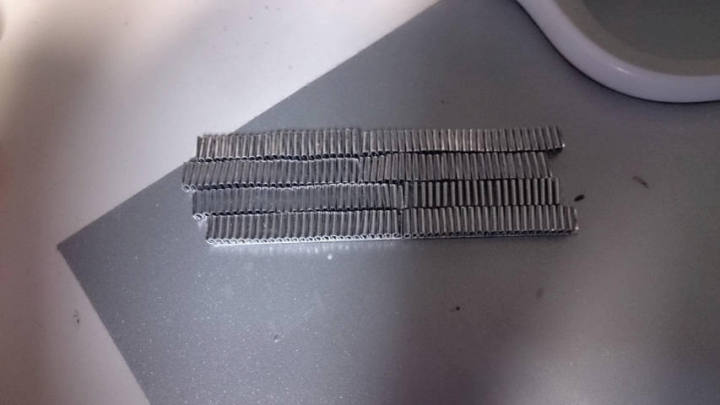
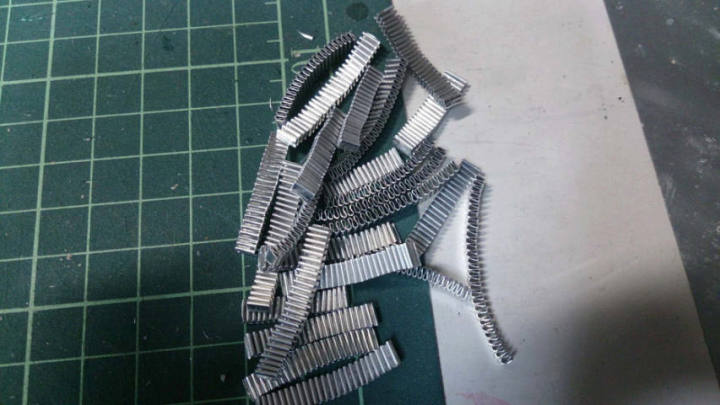

11.やっぱりどうやってもオリジナルより見た目が悪くなる。今回は諦めて、素直に墨入れですませます。
(再製作)
1.先日、ラジエータのディテールアップを断念することを宣言しました。
2.しかし、よくよく考えると内側の処理をしなければならない!結局は、二度手間!
3.
ラジエータのディテールアップを再開することにしました。
4.準備したもの「TAMIYA SINGLE GEARBOX」、0.1 mm 厚アルミ板、0.3 mm 厚アルミ板。
5.幅は 4.0 mm にしました。
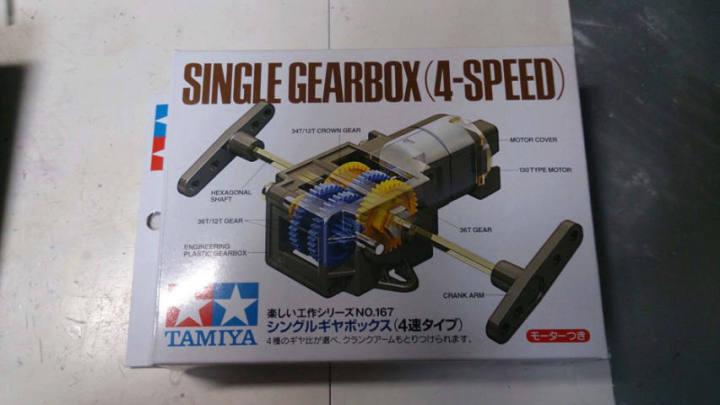
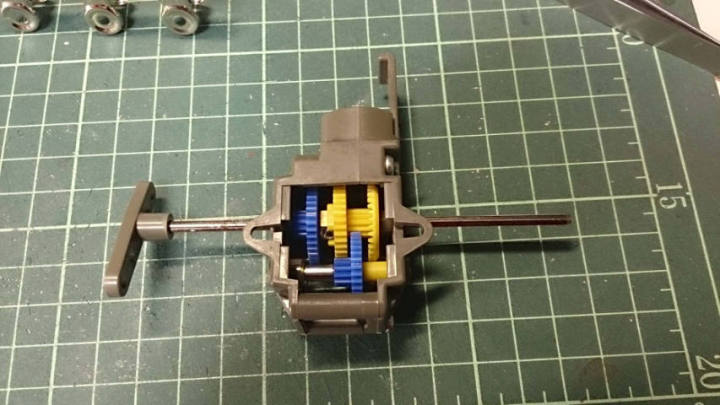
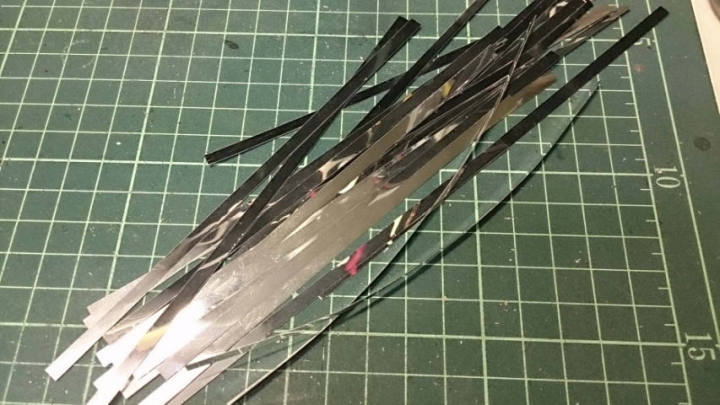
6. 0.1 mm 厚アルミ板を GEARBOX を使って折り目を付けます。
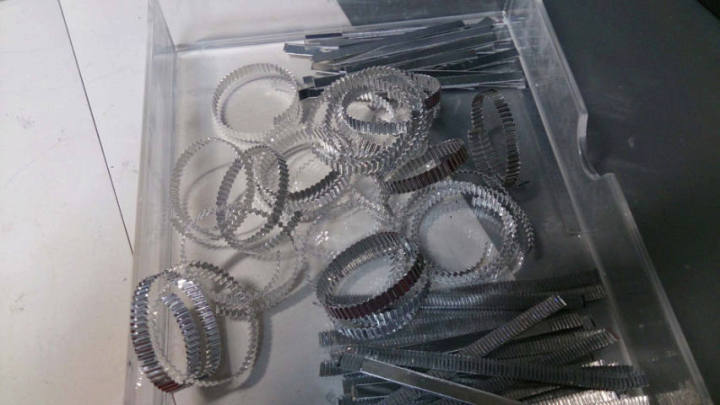
7.ピンセットを使用して折り目を整えます。
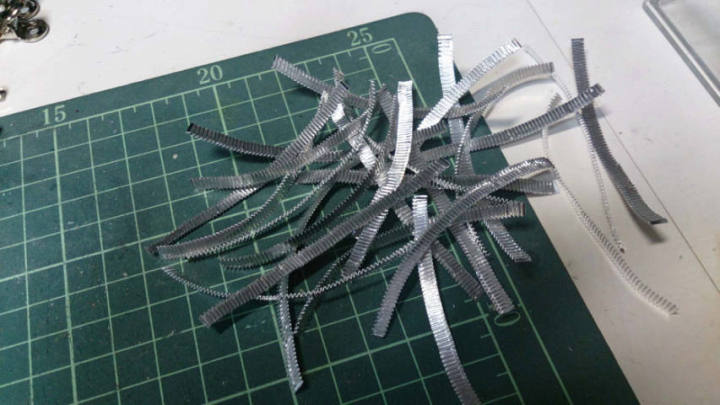
8. 0.3 mm 厚アルミ板と 0.1 mm 厚アルミ板をエポキシ接着剤で接着します。
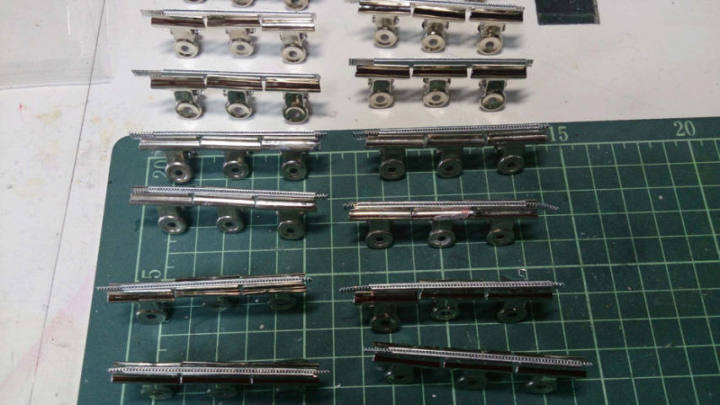
9.ラジエータ・コアを1段ずつ製作します。沢山作ります。もちろんあまるくらい。
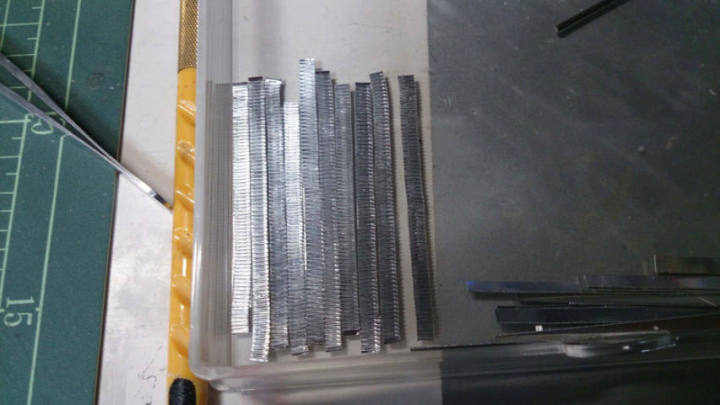
10.出来の良いものを集めて、コアに使用します。
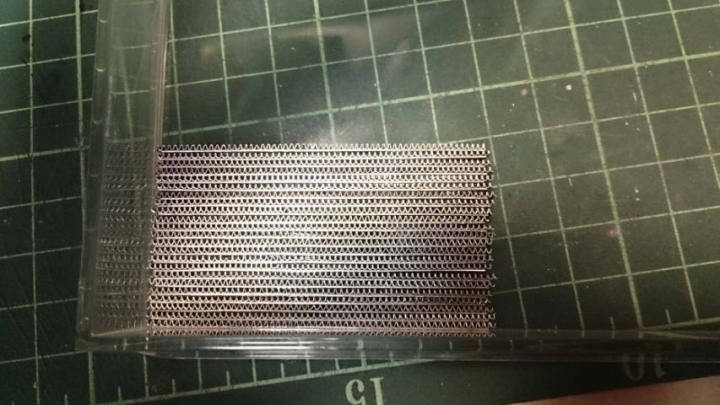
11.オリジナル・コアと比べてみます。
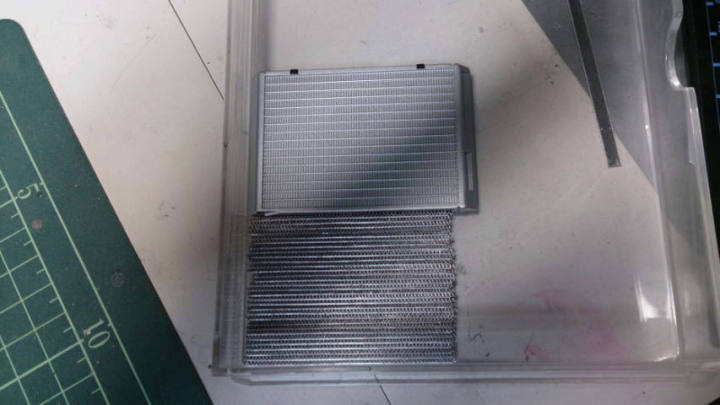
12.オリジナルに、このコアを置き換えます。
13.オリジナルのコアの部分を削除します。
14.ラジエータはサイド・タンク式なので上下には厚いタンク存在しません。出来る限り薄く削ります。
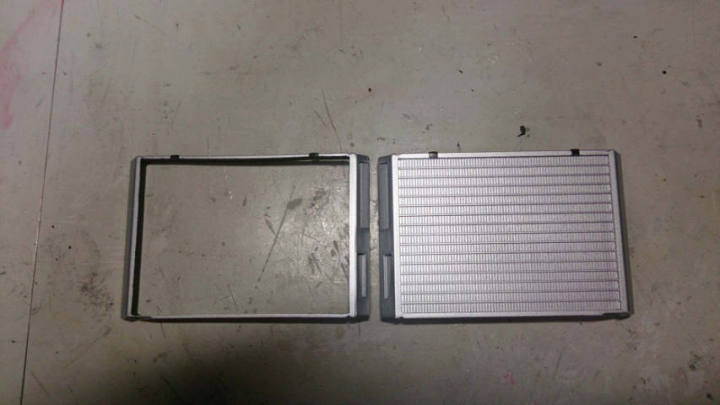
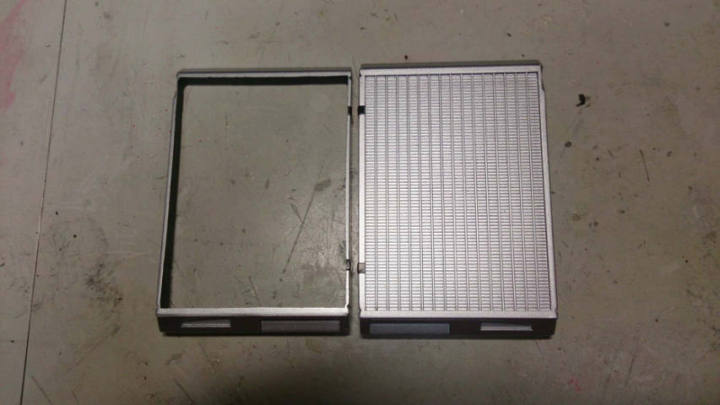
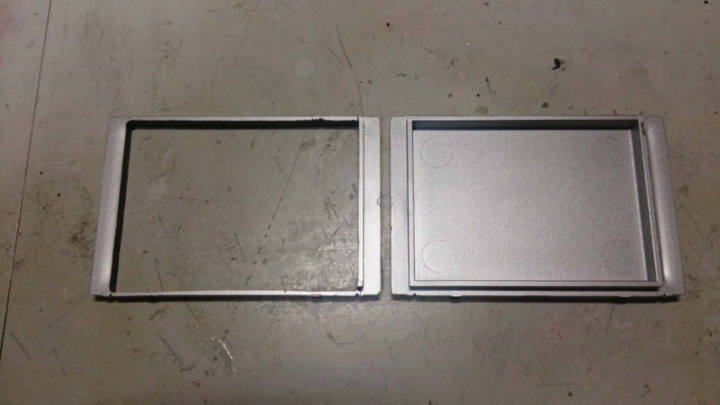
15.作成したコア一段ずつはめ込んでいき、完成させていきます。
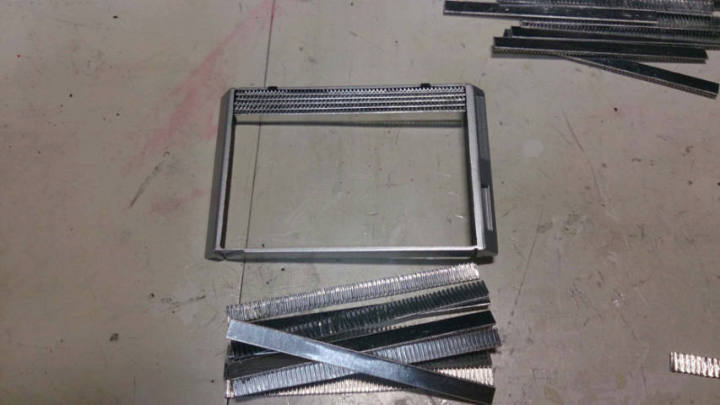
16.とりあえず、31段はめ込んだ時点でちょうど良い具合になりました。まだまだ接着はしていません。
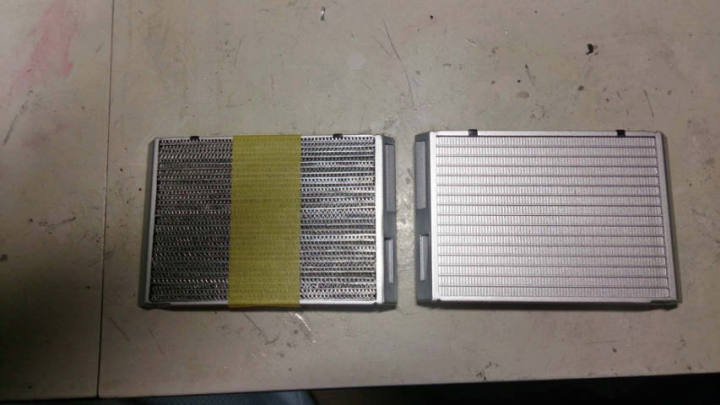
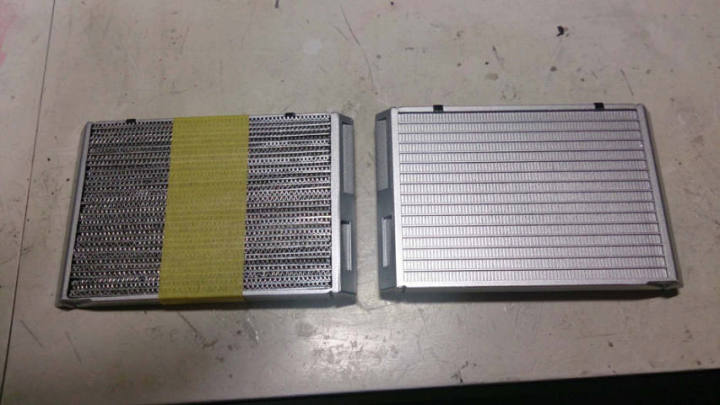
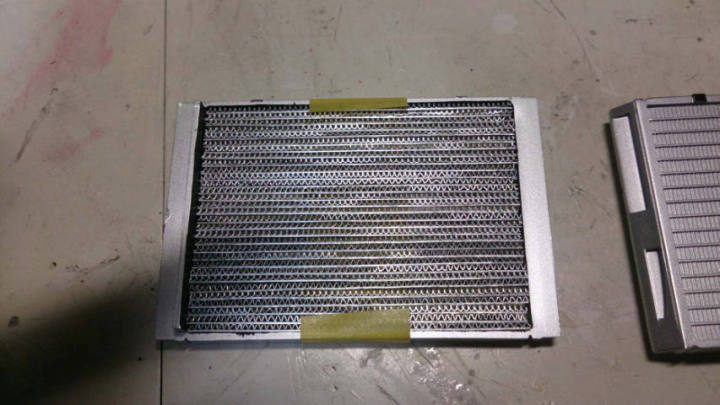
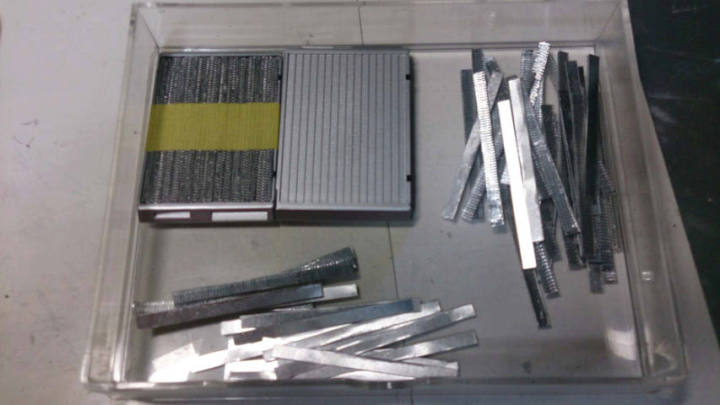
17.逆サイドも同じように製作します。
18.オリジナルのコアの部分を削除します。
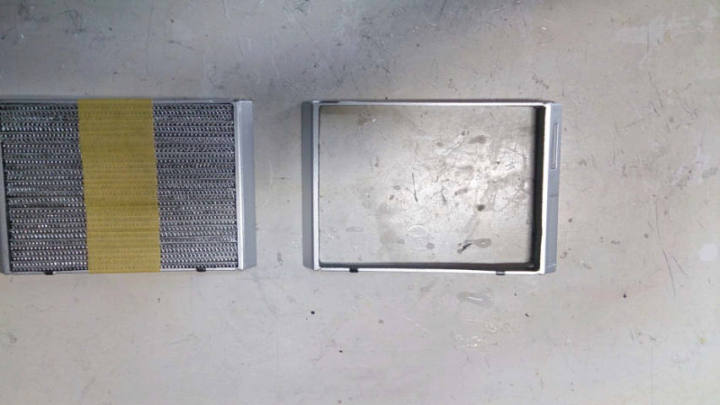
19.両サイドの部品製作が出来上がりました。
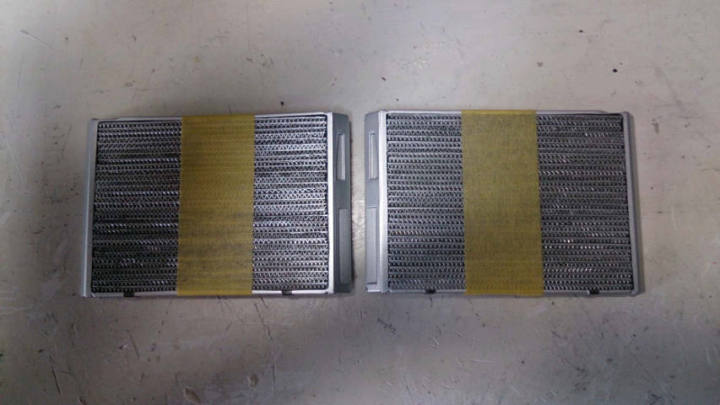
20.エポキシ接着剤でコアを接着し、完成しました。
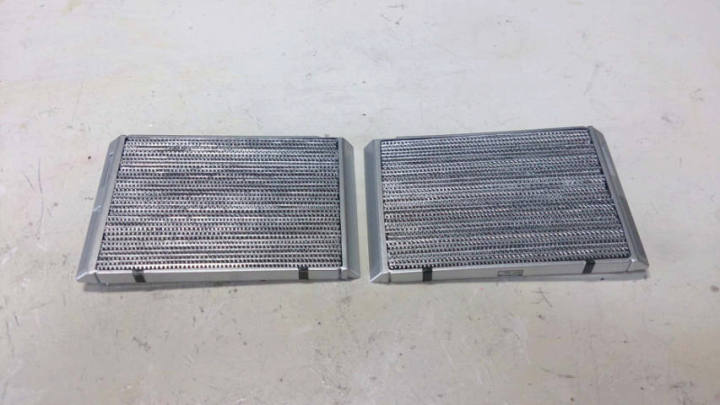
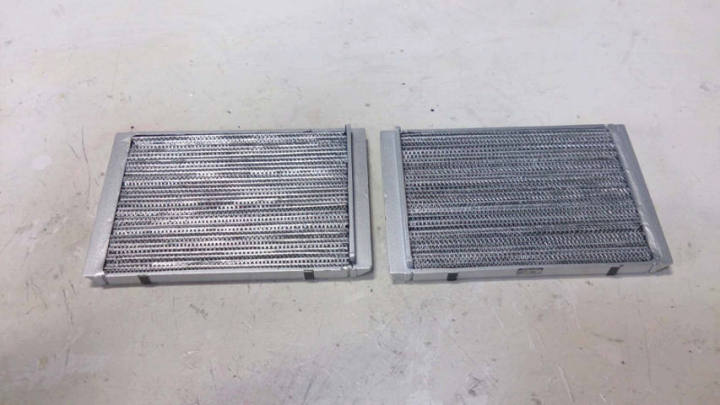
21.コアとタンクの部分の溶接表現を検討中。
フロント・ウイング翼端板ディテールアップ編
1. フロント・ウイング翼端板の厚さ!確認してみました。場所によって厚さが違う。左右の厚さが違う。さてどのくらいまで薄くできるでしょうか?頑張ってきます。
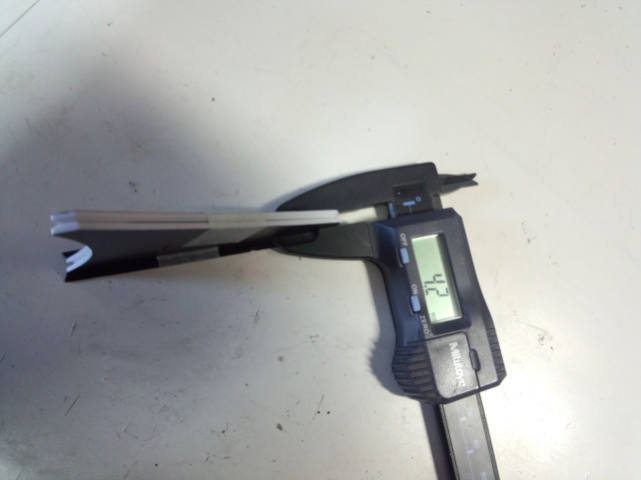
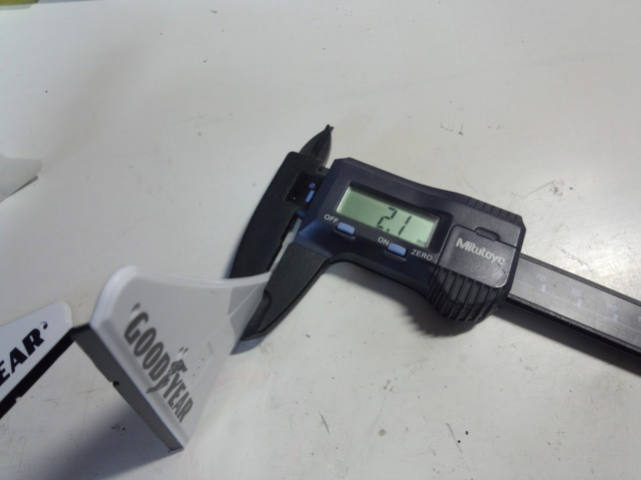
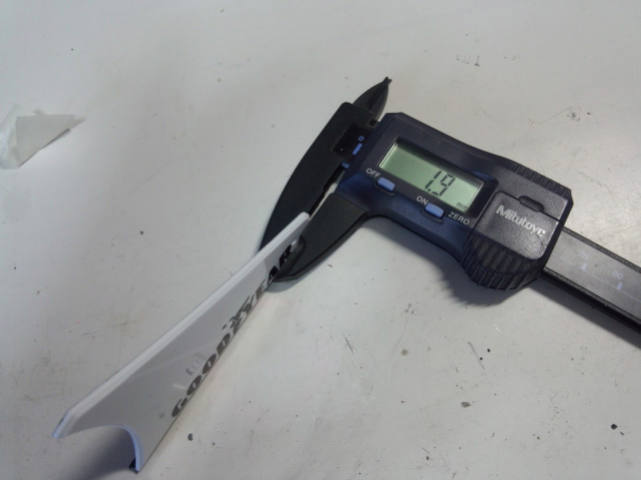
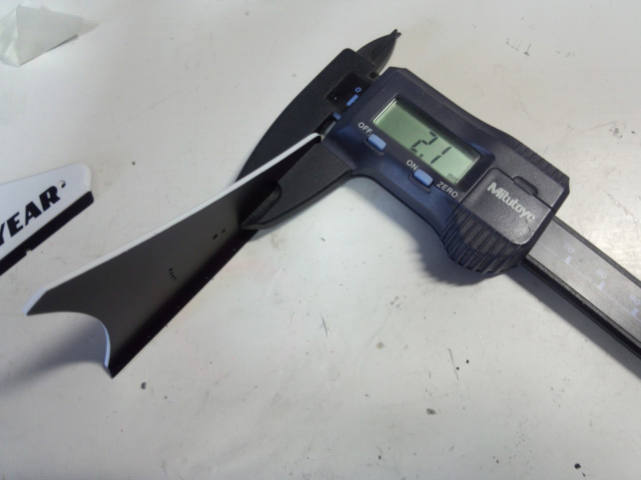
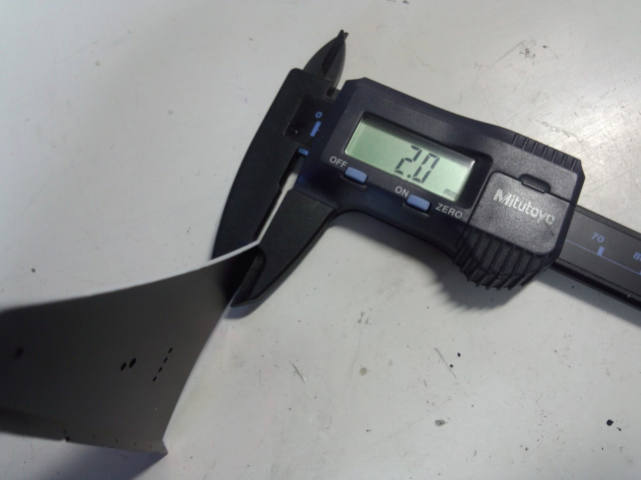
2. 先ず、精密屋ウレタンクリアを吹いてロゴの保護をします。クリアを吹きたくないところのマスキングをしました。
3.ディアゴスティーニの掲示板にはウレタンクリアとロゴの相性が悪いという報告がありました。少し怖いですが、人柱になります。とりあえず、マールボロ・デカールに関係ないところを吹いてみました。
4. 48 時間経過しました。完全硬化したウレタンクリアです。まだ研ぎ出しはしていません。
5.フロント・ウイング翼端板を内側から水研ぎし、厚さ 2mm から 約 1mm まで薄くしました。水研ぎには #120 を使用し、仕上げを #600 を使いました。
6.表側を #2000 出水研ぎ、50ミクロン・コンパウンド研ぎ、0.5ミクロン・コンパウンド研ぎ出しをしました。
7.表側をマスキングし、フィニッシャーズ・カーボン・ブラック・マットを吹きました。これで、気になった点を一つ解決出来ました。
.jpg)
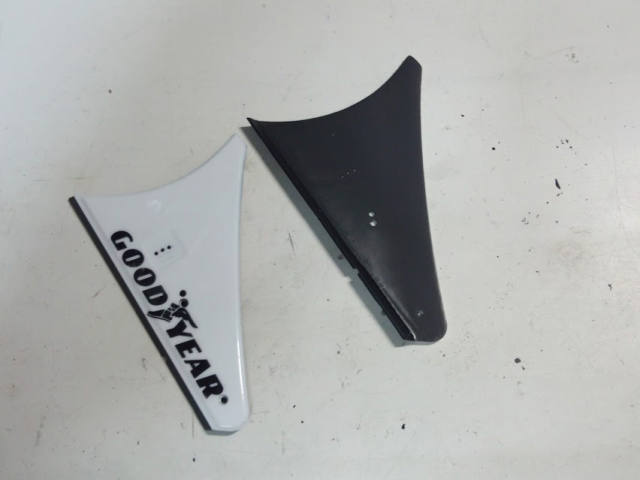
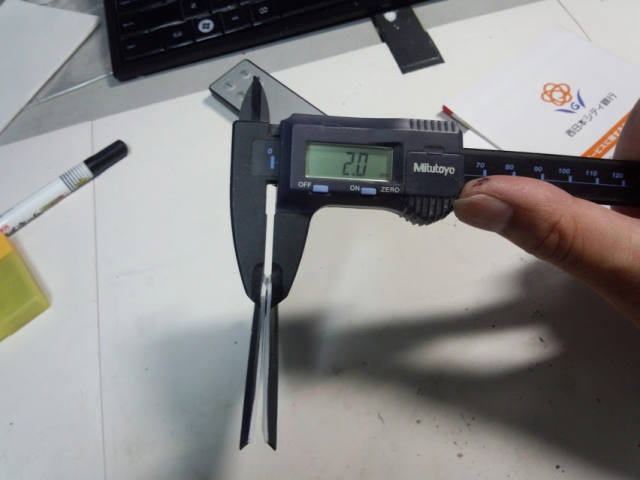
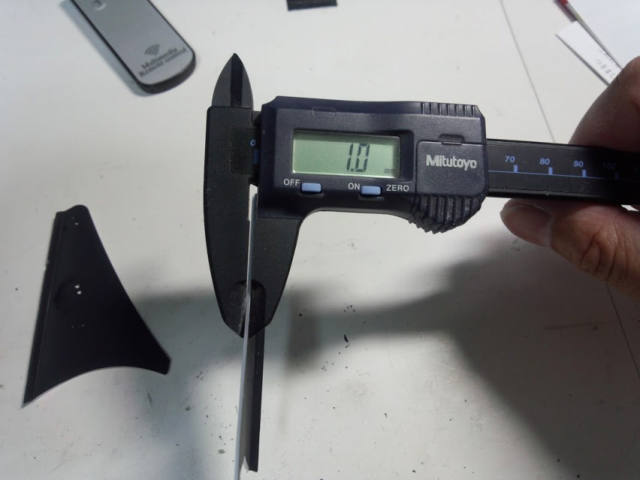
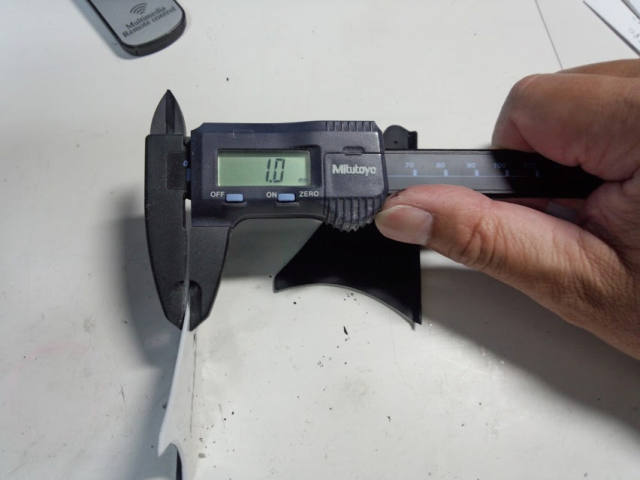
8.この翼端板、ねじ穴が大きすぎるので使えません。やっぱり、翼端板は自作することのします。
9.展示方法変更の為、この方法を採用することにしました。
リア・ウイング・ディテールアップ編(計画中止)
1.リア・ウイングも 3 セットディスプレイ用に製作を企んでいます。ただ、翼端板は簡単ですが、主翼やフラップが問題です。
.jpg)
2. 0.5 mmプラ版を使って、マスターを製作しました。
.jpg)
3. 0.5mmアルミ板で 3 セット翼端板原型を作りました。内側にはへーラインを入れています。
4. 0.5 mmプラ板で整流パーツを取り付けました。
.jpg)
5.リア・ウイング翼端板にホワイト・サーフェイサーを塗装後、フィニッシャーズ・MP4 RED を吹きました。
.jpg)
.jpg)
.jpg)
.jpg)
6.リア・ウイング主翼、フラップ、ステイをコピーしました。
7.展示方法変更の為、計画中止
フロント・ウイング・ノーズ・ディテールアップ編(計画中止)
1.先日、購入したフロント・ノーズ部分のデカール( Museum collection )が届きました。( 2 セット)使用するかどうかは解りませんが念のため、保管しておきます。尚初回特典で、木製のスキッドとタイヤ・マーキング・シートが入っていました。
2.フロント・ノーズのデカールが手に入ったので、フロント・ノーズ自体を自作出来ますね・・・。頑張って挑戦してみようかな・・。
3.今回の挑戦はフロント・ウイング主翼とフラップのコピーです。私は普段は 1/43 スケール・モデルを製作しているので、あまりレンジを扱うことがありません。レンジを使用してコピーをするのは初めての試みでした。試行錯誤の結果、やっと納得のいく作品が出来ました。
4.先ず、フラップですが一番右のものは片方に気泡が入り没にしました。その後、空気の抜け道を工夫して 2 セット使用出来る作品ができあがりました。
.jpg)
5.主翼は一番奥が最初に製作したものです。残念ながら気泡が入ってしまいました。後から盛りましたが、使用出来るかどうか?真ん中の作品は気泡は入っていませんが、少しシリコンゴムが歪んでいたので曲がっています。ディスプレイ用には使用できると思います。一番手前の作品は空気の抜け道を工夫した結果、納得のいく作品が出来ました。
.jpg)
6.翼端板も 3 セットほど製作中です。一番出来の良いものを使用するつもりです。
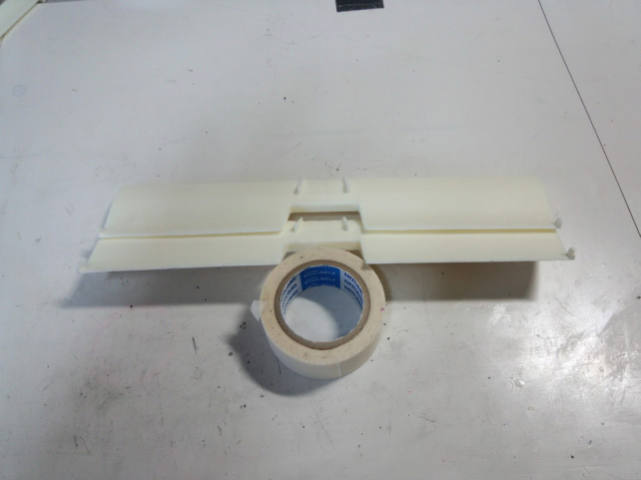
7.フロント・ウイング主翼の成形を行いました。主翼は 3 個とも使用できそうです。フラップの方は 1 セットだけ使用できる状態でした。
.jpg)
.jpg)
.jpg)
.jpg)
8.完成したモデルの横にフロント・ノーズを何個か展示するとディテール・アップにつながるので、 3 セットほど製作予定です。
.jpg)
9.フロント・ウイング、フラップ、ノーズの塗装が出来上がりました。
.jpg)
.jpg)
10.自作デカールを貼りました。
.jpg)
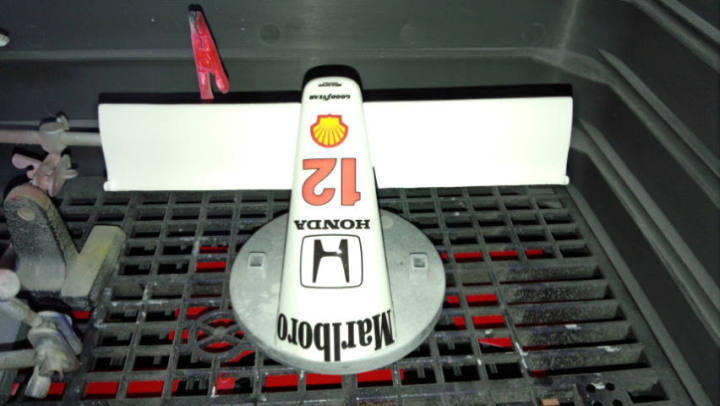
11.デカールが乾燥後、薄くクリアを吹きました。
12.精密屋ウレタンクリアを吹きました。
.jpg)
13.フロント・ノーズ、残りの製作を始めます。
.jpg)
14.ウレタン・クリア吹きまで終了しました。まだ研ぎ出しはしていません。ディスプレイ用なので造りは甘いです。
.jpg)
15.内側の処理をしてみました。全て違う方法で製作してみました。
16.カーボン・デカールは自作でレーザー・プリンタで印刷したものです。残念ながら、このインクがフィニッシャーズの塗料に耐えきれませんでした。よって、水性塗料を使いました。
17.一番左はクリア・シートに印刷したデカールを使用しました。よって、デカールを重ねてしまっては模様が、濃さが変わってしまいます。この選択は失敗でした。もちろん、下地を黒に塗った場合はカーボン模様は表現できません。このカーボン・デカールは別の場所で使用することにします。
18.一部、フィニッシャーズ・フラットコートを筆塗りしたため溶けてしまいました。後から、水性クリアを筆塗りし、何とが誤魔化しました。
19.真ん中と右側はホワイト・シートに印刷したものです。この場合、カーボン・デカールを重ねてしまっても、たいした影響は出ません。作業が格段に楽になりました。しかし、このホワイト・シートはデカールとしてはかなり厚すぎて、曲面には使えませんでした。
20.そこで、ノーズ先端部分は先につや消し黒で筆塗りし、後からデカールを貼りました。
21.また、このカーボン・デカールはあまりにも白すぎてしっくりしません。
22.結局、水性クリア・ブラックを筆塗りし、わざと斑を出しました。
.jpg)
23.ペーパーをかけて、表面を粗くしました。残念ながら、デカールが一部はげてしまいました。
24.次回は MD-5500 で印刷したデカールを使用することにします。(インクが溶けないので)
.jpg)
.jpg)
.jpg)
25.仮組しました。こんな感じです。翼端板の出来は満足いきましたが、それ以外の出来が納得いきません。3本製作しましたが、ノーズ、主翼、フラップ、もう一度最初から作り直します。どうせ、全部自作のパーツですから納得がいくまで何回でも作り直せます。
26.レンジの固め方も正確に計らないと堅くなりません。混合液が無駄になりますが、余裕を持って正確に計った方が出来よくなります。今回はノーズと主翼の間に隙間が出来たこと、フラップがきちんと固まらず、変形したので、 3 本とも全部作り直します。
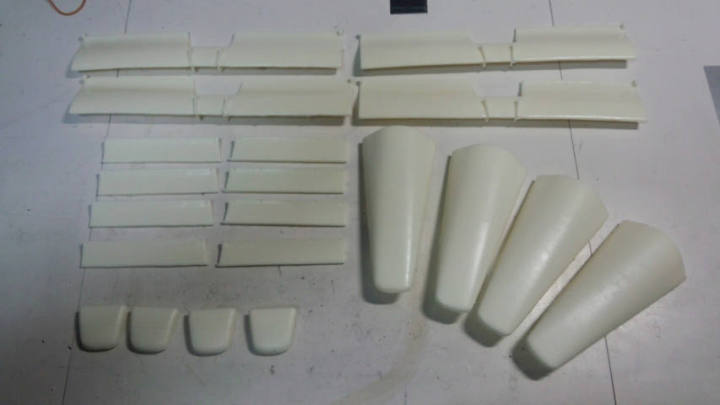
27.再度、フロント・ノーズを製作にかかります。今度は前回の失敗を生かして、丁寧に製作します。
.jpg)
28. 4 セット組みました。もちろん主翼、フラップ後端は薄く削りあげました。この後、パテ埋めをして表面を整えます。
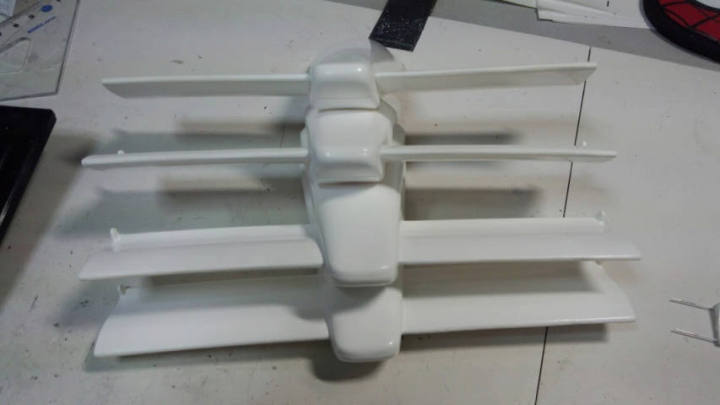
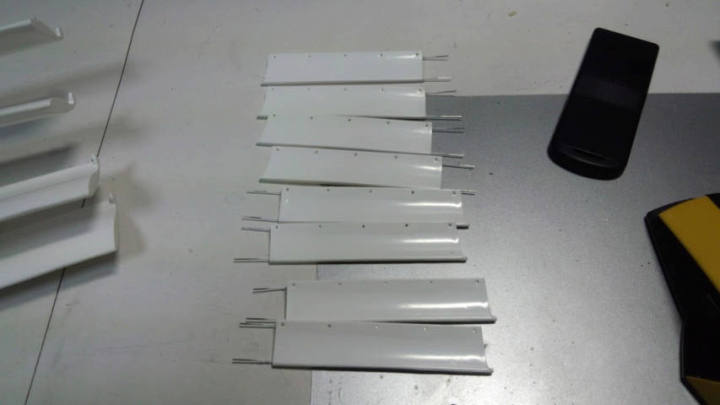
29.表面処理をした後、ホワイトサーフェイサーを吹きました。その後ペーパーを掛けました。
30.フィニッシャーズ・ファンデーション・ホワイトを 3 回ほど吹きました。フラップはデカールがはれる状態になりましたが、ノーズの先端のラインがまだ消えません。もう一度処理をします。
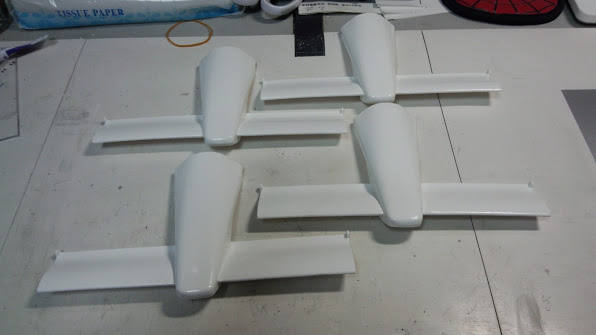
31.あれからペーパーをかけたり、ホワイトを吹いたり繰り返し。やっと納得のいくものが出来ました。これからデカールを貼ります。
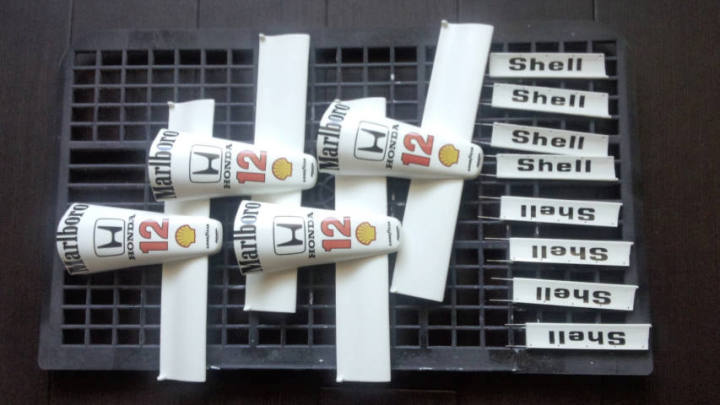
32.デカールを貼りました。一部、デカールの皺、破れがあったので貼り直しました。レーザー・プリンタで印刷したカラー・デカールはウレタンクリアに耐えられないので、薄く水性クリアを吹きました。やはり、MD-5500 で印刷したモノクロ・デカールの方が作業しやすいですね。
33.展示方法変更の為、計画中止
エンジン・ブロック・結晶塗装・ディテールアップ編
1.今回は結晶塗装の実験をしてみました。オリジナルの方法です。上手に出来るか解りませんが・・・。
2.道具は耐熱ブロック、爪楊枝、簡易ライター・バーナー、水性塗料。注意点は油性塗料を使用すると引火する場合があることですね。
.jpg)
3.結晶塗装したい場所をバーナーで暖めます。その上に水性塗料を乗せて、再びバーナーで炙ります。
4.長所は塗装をしたい場所を細かく塗り分けることが出来、後で処理をし直すことが出来ることです。
5.短所は塗料を直接加熱するので、結晶塗装と言うよりお焦げという感じですね(笑い)
6.このまま組み立てるかどうか思案中です。もう少し上手く表現出来るか試行錯誤中です。
.jpg)
.jpg)
.jpg)
.jpg)
7.納得がいかないので、再挑戦しました。注意点はさっきと違って結晶塗装したいところに最初塗料を乗せます。その後、塗料が焦げないように遠目からゆっくりバーナーで暖めることですね。急激に、温度を上げると失敗します。そのあたりは試行錯誤で要領を得るしかないですね・・・・・。
8.とりあえず、ヘッドカバーは我慢出来る範囲まで仕上がりました。エンジン後方の処理は駄目ですね。もう一度頑張ってみます。
.jpg)
.jpg)
.jpg)
9.やっぱり駄目だ!根本的に塗装が燃えてしまうため、結晶塗装とはほど遠いです。温度が上がりすぎてしまうので、効果が得られません。素直にオーブンを使った方法が一番良いようです。ただ、私の家にはオーブンがないので、別の方法を考えます。もし、駄目な場合は結晶塗装を諦めます。
10.現時点では結晶塗装に成功しておりません。もう少し研究させて下さい。
11.やっと結晶塗装ができあがりました。上手くいかなかった原因を究明することに成功しました。
12.準備したものはオーブンが無いので、アクリル板を曲げるために使用するヒーターを準備しました。そのままではパーツを置きにくいので、アルミ板を使ってテーブルを作りました。その上にパーツを載せて、熱を入れます。
.jpg)
13.今まで上手くいかなかった原因は爪楊枝を使用したことです。つまり、塗料の溜まりができ大きな気泡になります、そのまま蒸発するので見た目が悪くなっていました。
14.そこで、筆を使い少量の塗料を何回かに分けて薄く塗り重ねていきました。今度は、きめの細かい縮が出来、成功したと思います。これで一つ大きな問題が解決出来ました。
.jpg)
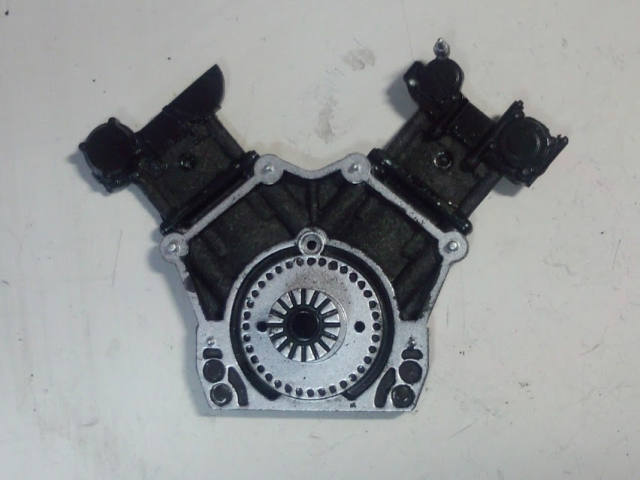
15.完成品にこの塗装を採用するか再考中。
カーボン・ブレーキ・ローター・ディテールアップ編途中経過
1.以前より気になっていたカーボン・ローターを改造してみました。一見、立体感が足りないので・・・・。
2.先ず、ベルハウジングとローターの間に隙間を彫り込みました。実車では正面から見ると隙間は見えませんが、より立体的に見えるようになったと思います。
3. ホイールのボスが刺さる穴を貫通させました。
4.ベルハウジングとローターを固定する六角ボルトを「Adlers Nest製」ステンレス六角ボルトに置き換えました。
5.ボルトの緩み止め用のワイヤーを導線をほぐしたもので製作しました。
6.前後のローターを合わせたときの隙間が気になるので、接着剤で隙間を埋めたあとつや消し黒で塗装しました。もちろん後ろのローターも余分なところは削り取りました。
.jpg)
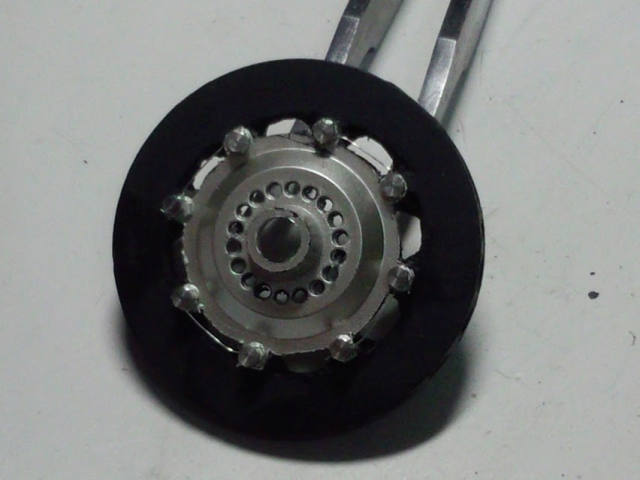
.jpg)
.jpg)
.jpg)
7.上記の方法では納得いかないので、また試作しました。今回はオリジナル。パーツは使わず、コピーしたもので試作しました。
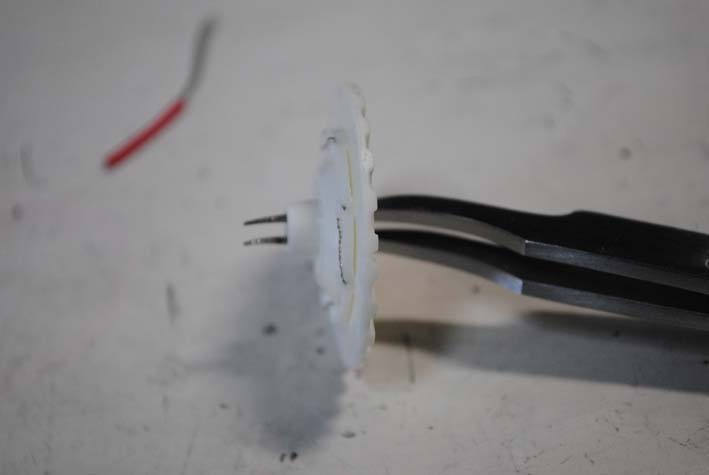
8.エッチング・ソーでローターとベルハウジングの間に隙間を彫り込みました。正面から見ると全然意味のないことですが、拘ってしまいましました。ただし、この方法だとローター面に傷が入るのであまりお勧めしません。どちらにしろ、ローターは後で塗装するので、大きな傷だけを気をつけることですね。
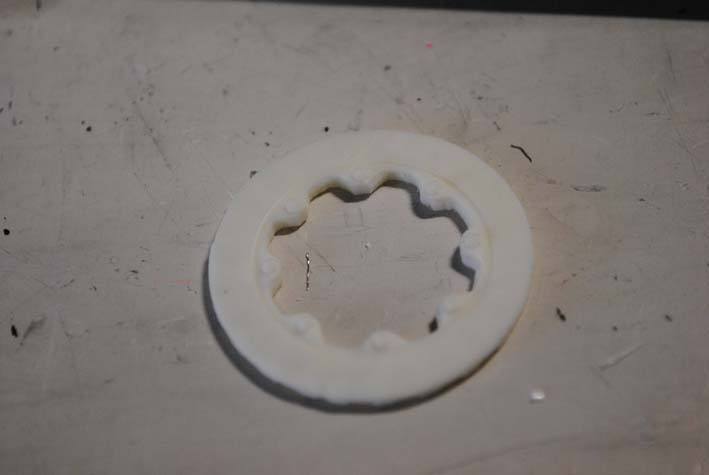
9.ローター内側の不要な部分を削りました。これも、見えないところなのであまり意味がありません。
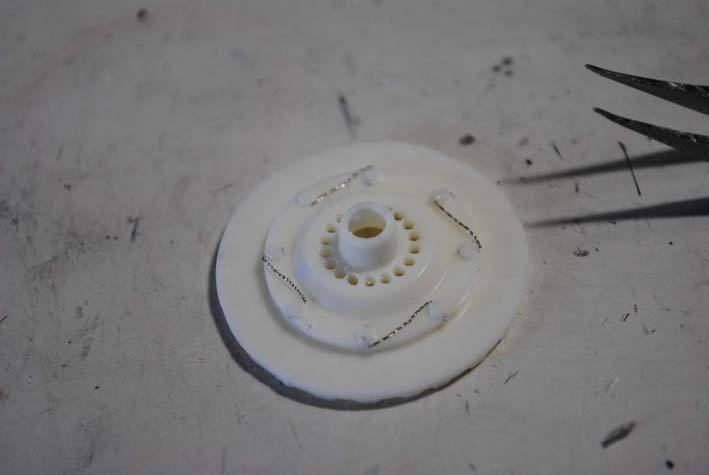
10.ボルト緩み止めの縒り線を取り付けました。この作業は慎重に!先ず、 0.3 mm ピンバイスで穴を開けます。その後、 0.5 mm のピンバイスで穴を大きくします。このサイズであれば 2 本の縒り線が通せます。
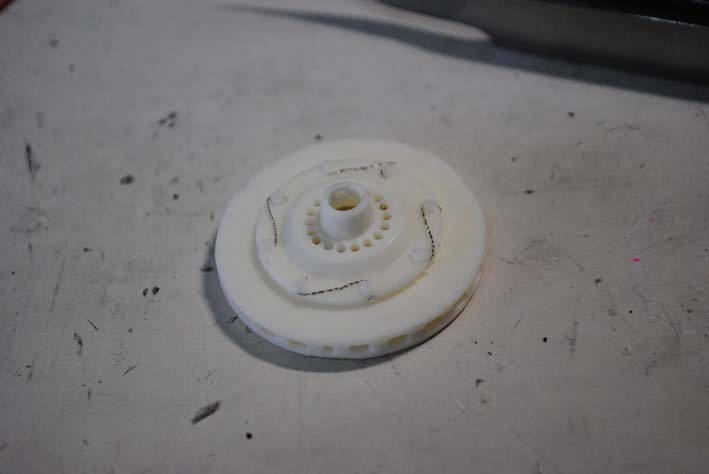
11.この後ローターを接着し、隙間を埋めてローターを塗装します。
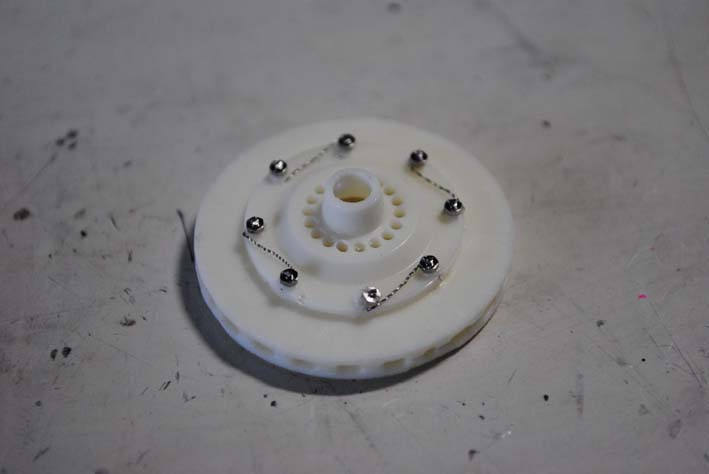
12.最後にボルトをメタルパーツに置き換えます。
13.以前一度挑戦してみましたが、ちょっとやり過ぎ感が出て実車から遠く離れてしまいました。
14.今回は、コピーを製作し試作した上でオリジナル・パーツを組み立てました。
15.試作品とは少し変更点があります。
16.ベルハウジングの穴は 1.2 mm のピン・バイスで開けました。
17.ベルハウジングとローターの間にエッチング・ソーを使って溝を彫り込みました。これで少し立体感が出ました。
18.ボルトの緩み止め用のワイヤーを縒り線にしました。
19.ボルトにの根本に 0.5 mm ピン・バイスで穴を開け、ワイヤーを通しました。
20.ローター前後を合わせたラインを消すために、接着した後塗装しました。
21.初めはローター面全部を塗装しましたが、どうしてもローターそのものが厚くなりキャリパーとの隙間が心配になりました。
22.そこで、逆にローター面の塗装を削り取りました。パーツが ABS
樹脂で出来ているので、カーボン・パーツのようになり結果オーライでした。
23.最後に、ボルトをメタル・パーツに置き換え、立体感を強調しました。
.jpg)
24.ボルト、メタルパーツ置き換えについて、再考中。
フロント・ウイング・スキッド自作編
.jpg)
1.木製スキッドを自作しました。材料にはいろいろ考えた結果、アイス・バーの木がちょうど良いようです。厚さはそのままで、リューターで溝を掘るだけで簡単です。おおざっぱに試作しました。後は取り付けるとき細かな修正をします。
.jpg)
.jpg)
2.自作翼端板、第 1 号完成しました。裏側はヘアーラインを入れて、フィニッシャーズ・カーボン・ブラック・マットを吹きました。
3.自作スキッドを接着剤で貼り付け、8 カ所ピンで固定しました。
4.スキッドをクリアで塗装しました。
フロント・ウイング・翼端板自作編(計画中止)
1.フロント・ウイング翼端板を自作することにしました。せっかく製作するなら後で何枚も製作出来るようにマスター型版を 0.5mm プラ板で最初に作りました。
.jpg)
2.マスター型版を使用して、 0.3mm アルミ板、 0.5mm プラ板、 0.2mm プラ板を切り取りました。
.jpg)
3.それぞれを接着し、フロント・ウイング主翼取り付けよう穴あけ、フラップ取り付けよう穴あけ、フラップ角度調節用穴あけをおこないました。本日はここまで、後はパテ埋めをして、成形します。
.jpg)
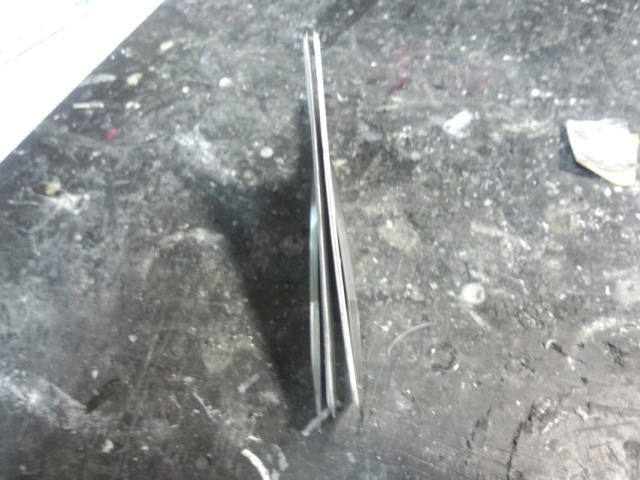
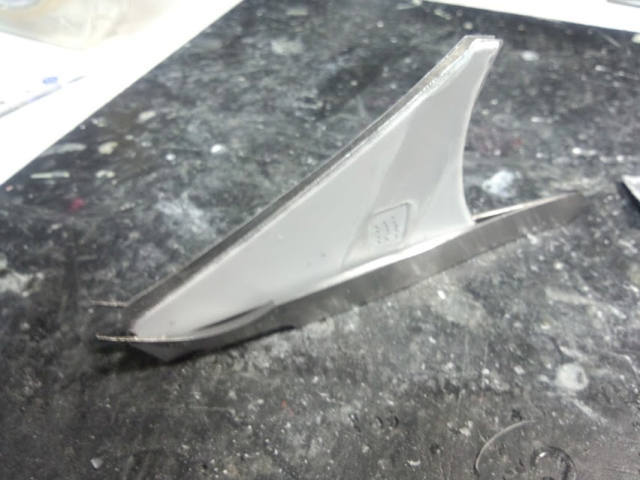
4.パテ埋めをして成形しました。この後サーフェイーサーを吹いて、再度成形します。

5.サーフェイサーを吹いた後、成形し直しフィニッシャーズ・ファンデーション・ホワイトを吹きました。フィニッシャーズ・カーボンブラック・マットを吹いた後、表に薄くクリアを吹きました。
.jpg)
.jpg)
6.自作したデカールを貼りました。上が先日改造した、ディアゴスティーニ製の翼端板です。下が今回全て自作した翼端板です。まだ、デカールを貼っただけで乾燥していません。この後薄く水性のクリアを吹いた後、ウレタンクリアを吹き完成させます。
7.試行錯誤編で紹介した方法で、フロント・ウイング翼端板を 3 セット製作しました。
.jpg)
8.ノーズの部分が出来上がったら、細修正します。
.jpg)
.jpg)
9.フロント・ウイング翼端板 3 セット完成しました。
10.スキッドの固定に使用したリベットのサイズをワンランク大きなものに交換しました。
11.展示方法変更の為、計画中止
タイヤ・マーキング・ディテールアップ編(計画中止)
1.先日購入した、ミュージアム・コレクションのデカール。初回特典で付属していたタイヤ・マーキング・シート、「GOOD YEAR 」の書体が斜体になっていて使えません。(スキッドもとても使えるものではありませんでした。)そこで、 1/8 スケールでマーキング・シート用のデータを自作しました。 PDF でダウンロードできるようになっています。カッティング・マシーンなどをお持ちの方はどうぞ自由に使用して下さい。下の PDF をクリックするとダウンロードできるので保存して下さい。
GOOD YEAR PDF
2.データを製作しましたが・・・・。タイヤ・ウォールの凹凸が表現できないので、画期的な方法が考えつかなければオリジナルのままでいきそうです。
3.新品タイヤ及び、見た目重視の為オリジナルで息ことにします。計画中止
自作デカールについての考察
私はデカールを失敗したときのために、自作しています。プリンタは ALPS MD-5500 と EPSON のカラー・レーザー・プリンタを使用しています。
ALPS MD-5500 はデカール製作用プリンタとしては最高のマシンです。ところが使いこなすにはかなりコストが高くつきます。残念ながら、もう新品を手に入れることが出来ません。純正修理も2015年までの対応で終了です。私も中古を手に入れて使用していましたが、先日とうとう故障してしまいました。しかし、純正修理がまだ出来るので直ぐに出しました。(純正ではない修理ショップさんもあるので、助かります。)
弱点はプリンタ・ドライバが正規には Windows Xp までの対応と言うことです。もちろん、色々工夫をすれば、 Windows 7 Ultimate 64bit の Xp mode でも動かすことは出来ます。しかし、私はこのプリンタ専用の Windows Xp PCを作りました。次に Adobe Illustrator が必要なことです。これはかなり高くつきます。ほかにもいくつかありますが、最高のマシーンであることには変わりありません。
インクジェット・プリンタについて
.恐らく誰もが挑戦すると思いますが、インクジェット・プリンタでデカールを作成することです。.私も一度は挑戦してみましたが、その当時印刷できるシートは 1 種類しかなくもちろんホワイト・デカールは作れませんでした。インクジェット・プリンタの性能も良くなく、直ぐにインク詰まりを起こしインクジェット・プリンタの価値を見いだせませんでした。(結局、現在もインクジェット・プリンタは所有していません「インク代も馬鹿にならない」)
さて、デカール用シートについてですが、私が使用しているシートは3種類です。
WAVE NEW クリアデカール B5 ( 182 mm x 257 mm ) x 5 枚 OF-003-1200 1,260 円
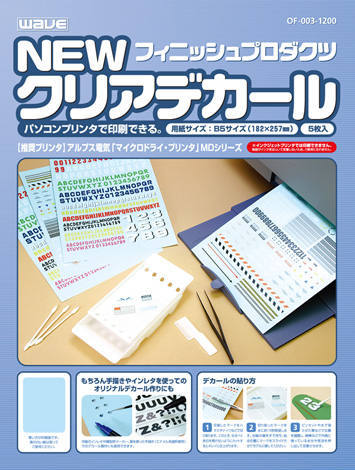
MYK DESIGN 水転写式クリアなデカール A4 ( 210 mm x 297 mm ) x 2 枚 598円
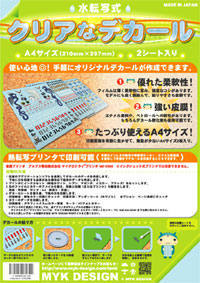
Fine Molds CLEAR DECAL A4 ( 200 mm x 280 mm ) x 2 枚 DC01 609円

Fine Molds WHITE DECAL A4 ( 210 mm x 297 mm ) x 2 枚 DC02 798円
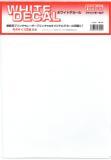
11.それぞれ利点欠点があります。それでもベストは WAVE ですね。ところが、Fine Molds はレザー・プリンタ対応を謳っています。これはかなり便利です。
12.それではそれぞれの利点欠点を私の経験から書き出します。それぞれの場合によって使い分けをすると良いでしょう。
WAVE NEW クリアデカール
対応プリンタ:事実上 MD-5500 のみです。
シートの厚さ:薄くて貼ったとの研ぎ出しもし易い。
水転写:水につけたときの剥がれやすさが良い。
耐久性:ウレタン・クリアにも問題なく使用できます。
サイズ:B5 だということが少し使いにくいです。他のメーカとサイズが違うため。
その他:インクが CMYK なので、それぞれの単色、白、黒、メタリック・ゴールド、メタリック・シルバーを使用する場合はよいが、 CMYK が混合するとドットが目立ってしまいカラー・デカールにはむかない。
MYK DESIGN 水転写式クリアなデカール
対応プリンタ:MD-5500 と何故かレーザー・プリンタが普通に使えます。
シートの厚さ:薄くて貼ったとの研ぎ出しもし易い。ただし、破れやすい。
水転写:水につけたとき剥がれるまでかなりの時間を要し、作業しにくい。
耐久性:ウレタン・クリアにも問題なく使用できます。レーザー・プリンタの場合は水性クリアを上塗りすること。
サイズ:A4
その他:恐らく台紙が厚く、デカール・シートとの接着が強いためレーザーでも印刷できるものと思われる。逆に、水転写がしにくい。
Fine Molds CLEAR DECAL
対応プリンタ:MD-5500 とレーザー・プリンタが使えますが、レーザーの場合A4全面を一度に印刷は出来ません。インクの定着が悪く、少しずつの印刷しか出来ません。
シートの厚さ:かなり厚くて研ぎ出ししてもなかなか平面にならない。
水転写:薄くて貼ったとの研ぎ出しもし易い。
耐久性:ウレタン・クリアにも問題なく使用できます。レーザー・プリンタの場合は水性クリアを上塗りすること。
サイズ:A4 近似
その他:ウレタン・クリアでの研ぎ出しはかなり骨が折れます。クリアの塗料は選んだ方が良いでしょう。
Fine Molds WHITE DECAL
対応プリンタ:MD-5500 とレーザー・プリンタが使えますが、レーザーの場合部分的にインクの定着が悪くなるときがあります。
シートの厚さ:かなり厚くて研ぎ出ししてもなかなか平面にならない。
水転写:水につけたときの剥がれやすさが良い。
耐久性:ウレタン・クリアにも問題なく使用できます。レーザー・プリンタの場合は水性クリアを上塗りすること。
サイズ:A4
その他:ウレタン・クリアでの研ぎ出しはかなり骨が折れます。クリアの塗料は選んだ方が良いでしょう。
結局、 WAVE クリア・デカールを主に使用し、そのほかはケースに応じて使い分けています。